
Connect adaptivity directly: SKEDD direct connection technology brings new flexibility to device design
SKEDD direct connection technology makes device design more flexible
Whether modern climate and ventilation systems in building technology or compact controllers in classic industrial applications, intelligent automation structures require functionally embedded systems. This poses a challenge to device manufacturers to develop universally operational solutions for specific tasks and ambient conditions. SKEDD direct connection technology revitalizes PCB connection technology.
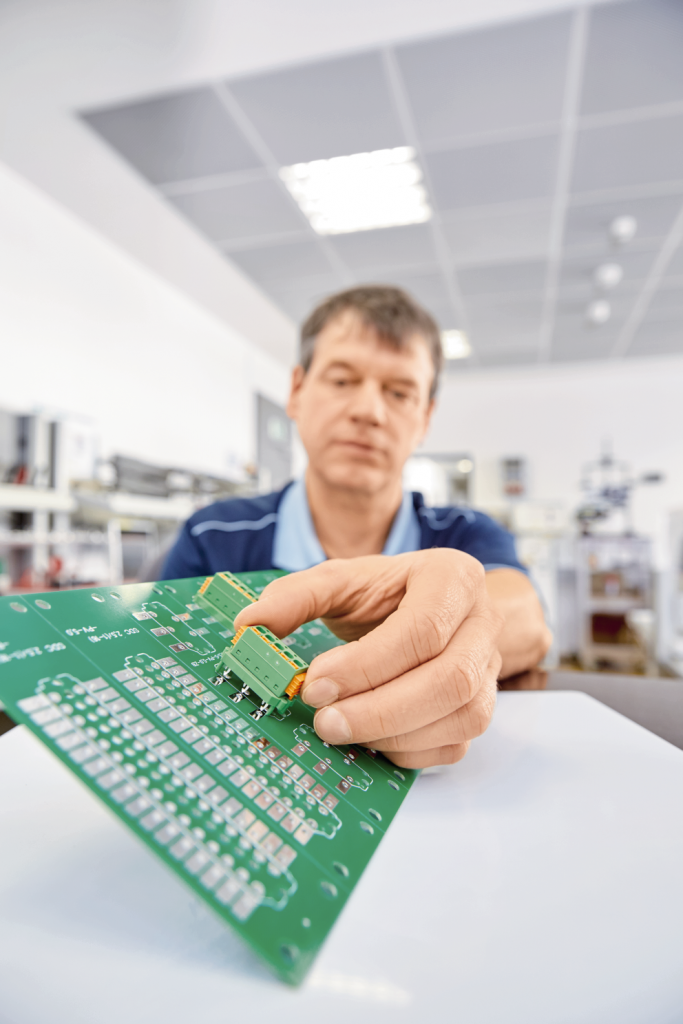
The first direct connector in the world with Push-in spring connection allows application-specific device designs with just a few PCB layouts
Increased device flexibility – that is to say, adaptability – means that fewer versions need to be produced and made available – and overall unit costs are lower. PCBs and connection components are the central nervous system of electronics and as such have a large impact on the performance and flexibility of electrical devices.
More flexibility thanks to SKEDD
The innovative direct connection technology SKEDD –Swedish for “it happened” – makes direct pluggable and detachable PCB connections at any position on the PCB possible for the first time. The SKEDD connector types SDDC 1,5 and SDC 2,5 from Phoenix Contact no longer require headers – they can be plugged in via tin-plated through-connection bore holes by hand. The advantage: In the past, the electronics manufacturer needed to combine application-specific connection technology such as PCB terminal blocks or headers with the PCB using an irreversible soldering process. This largely dictated functionality of the PCB and the overall device. SKEDD direct connection technology makes this process unnecessary; only the corresponding bore holes need to be provided in PCB manufacturing process. In this way, the PCB does not become thermally loaded again.
Currently, many PCBs are processed first in the SMD method, and PCB terminal blocks or headers are soldered on as the second step in the wave soldering process. If the second soldering process is removed, the operator saves process and component costs. This also makes all logistics and materials planning for the headers unnecessary. Equipment costs and feeder space requirements are also reduced when using the SMD soldering process. Accordingly, there is more space for additional components when the header is omitted using the SMD process. In an ideal case, additional modules can even be produced on a single system without conversion.
Reliable mechanical connection
Both PCB and device manufacturers see immediate benefits from this technology. In addition to saving costs, they are now able to use a single PCB layout for different device designs – and still implement flexible application-specific connections for signal, data or power transmission.
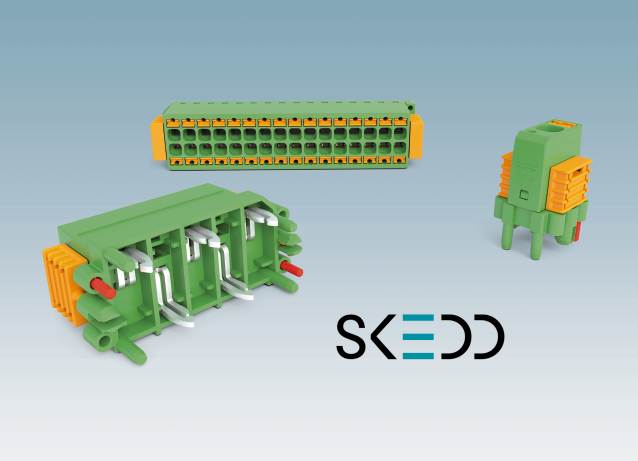
Single- and double-row direct connectors offer solutions for countless applications such as climate control systems, smoke and fire alarms or large household appliances
SKEDD contacts are an improvement on press-in technology, and they place no special requirements on the PCB. The contact zone consists of two flexible contact limbs that are easy to bend outward and that are adapted optimally to the plated-through bore holes. When inserting the contact into the bore hole, the contact limbs are pressed together – thereby ensuring a secure mechanical and electrical connection. Lateral body-bound rivets on the connector increase the mechanical stability as well. The interlock is designed for standard PCBs with a thickness of 1.6 mm and allows for up to 25 connecting cycles.
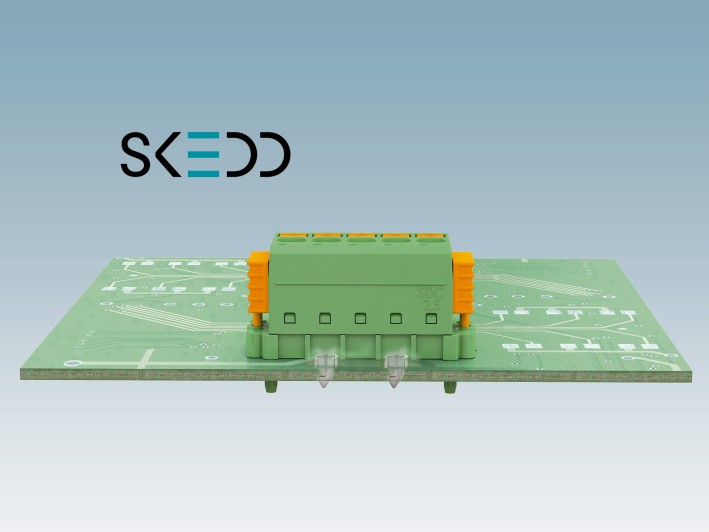
SKEDD contacts consist of two flexible contact limbs that are easy to bend outward and that are adapted optimally to the plated-through bore holes
Tests in accordance with the railway equipment and household appliances standards
In addition to the required approval and qualification tests, the SKEDD direct connectors from Phoenix Contact meet the highest requirements of mechanical and electrical safety. The series SDDC 1,5 and SDC 2,5, for example, are qualified for special fire protection requirements in accordance with DIN EN 60335-1 (“Household and similar electrical appliances – Safety”). Included in this standard are household appliances such as dishwashers, washing machines and portable cooking appliances, drives for awnings and blinds, heating units, climate systems and heat and cooling circulation pumps in private and commercial areas.
Two tests prove the capability of the electrical components and the polyamide insulating material used. First, a glow-wire with a temperature of 850 °C is applied to the material for 30 seconds. The Glow-Wire Flammability Index(GWFI) test is successfully passed if the test plate continues to glow less than 30 seconds after removing the glow-wire. The second test establishes the Glow-Wire Ignition Temperature (GWIT). For this test, a glow-wire with a temperature of 775 °C is held to the plastic test plate. The material may glow briefly, but for less than 5 seconds, and it may not ignite.
The SDC 2,5 single-row connectors are also qualified and approved for PCBs with HAL surfaces (Hot Air Levelling, surface protection) in accordance with DIN EN 61373 (“Railway applications – Rolling stock equipment – Shock and vibration tests”). These standards place high demands on the vibration-proof and shock-proof capabilities of devices and components used in trains. For this test, the connectors were exposed to 15 hours – five hours per spatial axis – of random vibrations with a frequency of 1 to 150 Hz and an effective acceleration of up to 5.72 m/s². Interruption of the contact may not exceed 1 µs during this process.
A wide range of solutions
The standardized tests attest to how reliable the direct connection technology functions, even under demanding ambient conditions and high safety requirements. SKEDD direct connectors are suited for classic industrial applications as well as for applications in building automation and railway technology.
The SDDC 1,5 and SDC 2,5 product series from Phoenix Contact offers solutions for countless applications such as climate control in rail vehicles, smoke and fire alarms or large household appliances. Both series feature tool-free push-in spring connection: This means that both solid and stranded conductors with ferrules can be connected without opening the clamping space. The integrated test points enable convenient function checks when loaded. Designed for conductor cross sections up to 2.5 mm², the single-row SDC 2,5 direct connectors are suited for currents up to 320 V. The double-row connectors from type SDDC 1,5 offer an efficient connection solution specifically for signal densities that are often high in measuring, control and regulation technology.

SKEDD direct connectors are suited for backside PCB connections, for example, or for internal device wiring
Summary
Tool-free, reliable and process-efficient – the combination of Push-in spring connection and SKEDD direct connection technology offers new flexibility in device wiring. SKEDD connectors do not require headers and can be plugged in directly by hand in tin-plated through-connection bore holes. This enables PCB and device manufacturers to implement countless device designs with application-specific connections for signals, data and power using just a few PCB layouts. Various tests have proven it: Whether for applications with high vibration requirements like railway technology or with special fire protection requirements like in household device technology – direct connectors with SKEDD technology are an interesting new solution.
Single- and double-row direct connectors
Phoenix Contact offers single- and double-row direct connectors with the series SDDC 1,5 and SDC 2,5.
The advantages at a glance:
Flexible positioning on the PCB
- Easy to plug in by hand and create vibration-proof connection
- Reduced component and process costs
- Tool-free, time-saving connection with Push-in technology
- Intuitive operation, thanks to color-coded push button
- Quick and convenient testing using integrated testing option
- Single- and double-row designs for up to 32 connection positions
|
SDDC 1,5 |
SDC 2,5 |
Contact arrangement |
Double row |
Single row |
Grid |
3.5 mm |
5.0 mm |
Current |
8 A |
12 A |
Voltage |
160 V (IEC)
300 V (UL) |
320 V (IEC)
300 V (UL) |
Number of positions |
2-16
(4-32 contacts) |
1-16 |
Conductor cross section (solid and stranded conductors) |
0.2 to 1.5 mm², AWG 24-16 |
0.2 to 2.5 mm², AWG 24-12 |
Feel free to contact us at marketing@phoenixcontact.com.sg to find out more!