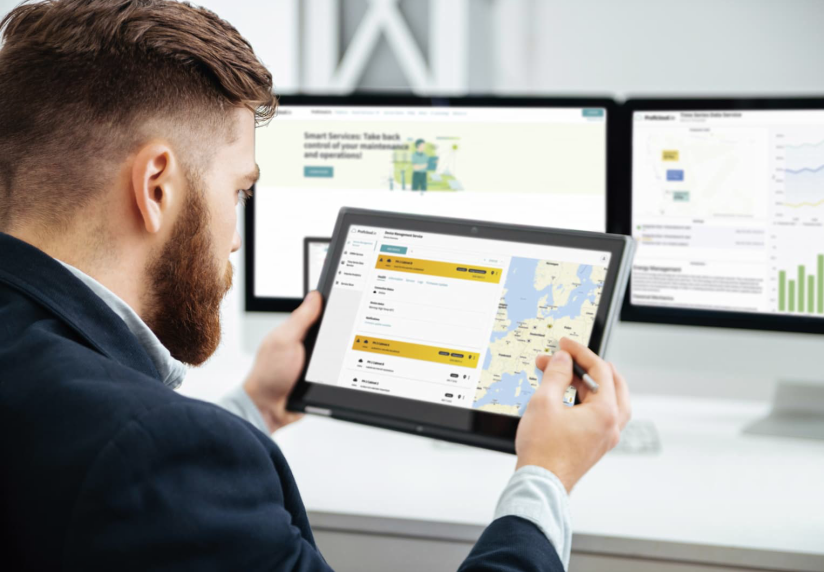
It is more crucial than ever for businesses to measure and analyze loads due to increased energy costs and strict legal obligations. Now, it is possible to complete this operation with IoT solutions that are simple to deploy with Plug and Play and accessible by IIoT platform and need for very little prior knowledge. Two instances from the production sector show how businesses might profit from this.
Prior to now, the energy consumption data that was included in the daily machine data had a minor function. That changed at the latest when the CO2 footprint became a significant KPI and energy costs increased significantly with less notice. All sectors that use more energy must now make the pertinent parameters measurable and analyze-able and show a continuous improvement in energy-related performance. Greater data transparency will be beneficial, particularly for small and medium-sized businesses (SMEs) that have up to now either utilized no energy monitoring at all or only very basic energy monitoring.
One reason is that companies can more easily comply with regulations and legislation and have a more thorough picture of how much energy certain machines, processes, or systems are using. They discover savings possibilities with the aid of this data, which in turn can help to raise energy efficiency and lower energy expenses.
Obstacles
However, finding a quick and accurate way to gather the essential consumption data is a challenge for those in charge of managing energy in businesses. For instance, smart meters installed on equipment and systems can often link to the IT infrastructure using communication protocols. Hence, they require more storage capacity, lengthy Excel lists, or appropriate analytics tools that, in the best-case scenario, may also assist with useful visualization. In other words, up until now, it took time and a lot of knowledge to connect various devices, record and analyze the necessary data, and then draw ingenious inferences from the findings. For energy managers, who frequently must work across numerous sites and with limited resources, this presents a significant issue.
Plug and Play connection to the cloud IIoT platform
This situation appears to have been created specifically for an IoT-based energy management system. Minimal IT resources can implement this kind of solution. Utilizing IoT-enabled measurement devices in the relevant control cabinet or at the machine/system, connecting them to a router, and creating an account with a cloud service are requirements. One such is the coupling of Phoenix Contact’s IoT-enabled EMpro energy measuring devices and the EMMA Service of the Proficloud.io IIoT platform. Energy Monitoring, Management, and Analytics is the abbreviation for EMMA. The smart service’s user-friendly interface makes it easy to visualize linked devices’ electrical energy and performance information. Regardless of where you situate the measuring devices, energy managers may access their data using this cloud-based system. The knowledge gained in this way permits the definition and use of appropriate measures.
The EMMA Service supports energy managers here in the check step of the PDCA (Plan, Do, Check, Act) cycle in accordance with international standard ISO 50001:2018 (Energy management systems – Requirements with guidance for use)
IoT-capable Through an Ethernet interface and Plug & Play using the TLS-encrypted MQTT protocol, EMpro energy measurement devices are immediately connected to the Proficloud.io IIoT platform. Energy managers may quickly and easily integrate the measurement devices into a new or current system using the free Device Management Service in the cloud environment. Automatically send and save the chosen measured devices. Energy managers now have access to this data and can use them directly thanks to the EMMA Service. Modbus or Profinet’s intricate settings, which were once common in industrial networks, are now a thing of the past.
Additional advantages of continuous energy data acquisition
Operational energy management is based on the continuously gathered energy consumption data of equipment, systems, and processes. They also offer the following further benefits:
- Optimize system utilization via intelligent component switching, balanced network loads, and the removal of harmonics.
- Smart trend calculations and load control can lower peak loads.
- Consistently monitor system parameters to reduce system downtimes.
Example applications from industry
Two examples explaining the EMMA Service functions:
Cold storage
Snack producer A aims to achieve CO2-neutral manufacturing and sustainably reduce energy costs, thus it would like to be able to see how much energy is used during cold storage and production. The company needs to be aware of two aspects in to determine the necessary energy efficiency measures and the procedures to reduce energy consumption: Let’s start with how much energy is now needed to cool a ton of potatoes that are kept in a cold storage facility. Second, it is also curious about how much energy is used to produce each kilogram of the goods it produces. The prior monthly meter read-out and Excel lists used to evaluate it took a lot of time and didn’t provide the transparency needed to meet A’s two objectives.
IoT-capable EMpro energy measurement devices now make possible the straightforward and comprehensive documentation of the energy data and the EMMA Service. The company enhanced its cooling based on the quantity of potatoes stored and streamlined the production process based on the knowledge gained. As a result of their connection to Proficloud.io, the energy management team has access to the worldwide sites and their energy data.
Bottling of beverages
Beverage company B has set a global goal reducing CO2 carbon emissions by 25% for the entire group. The first essential step to reaching this goal is to monitor and carefully control how much electricity, water, heat, and compressed the company is using. The beverage manufacturer deployed the necessary measuring equipment at the indicated primary loads for this reason, and Proficloud.io receives the measured data directly. The dashboard now allows the energy managers at B to quickly and easily visualize and analyze the loads there in real time. The goal of the firm leaders in the US is to prioritize providing comprehensive information on local, location-specific dashboards while also displaying the total energy consumption of all the Group’s energy sources on a worldwide dashboard.
This is exactly what the EMMA Service on the Proficloud.io IIoT platform can do. Proficloud.io also provides the opportunity to control the rights and duties of the employees inside a company using the User Management Service. Additionally useful is Proficloud.io’s Time Series Data Service, which analyzes extra data using freely customizable dashboards.
Access to newly implemented functions
Phoenix Contact, a full-service supplier in both cases, offers the hardware elements needed to connect to the cloud, including controllers, gateways, and energy-monitoring gadgets. The Proficloud.io IIoT platform and its standardized, scalable smart services, one of which is the EMMA Service, are accessible to the IoT-capable energy measuring devices in the EMpro product family. Phoenix Contact focuses on best-practice solutions that are simple to use, constantly evolve to meet client needs, and are based on the needs of regular business operations with its smart services. In conversations with users, new features and quick problem fixes frequently emerge. They also see the benefit of cloud-based services in general: As soon as newly added features and performance characteristics are available, existing users get direct access to them.