Fighting the climate crisis with series production
Power-to-X is a vital part of the energy revolution, aiming to replace fossil fuels with renewable sources. It involves converting renewable electricity into gases, chemicals, or fuels. PtG methods, particularly important for sector coupling, utilize existing gas infrastructure for storage and transport. The “European Hydrogen Backbone” envisions repurposing and expanding the infrastructure for hydrogen transportation. Automation and electrification strategies, such as Enapter AG’s AEM electrolyzers, are crucial for cost-effective and safe conversion processes. The installation of more wind and solar systems will further drive the transition to cleaner energy.
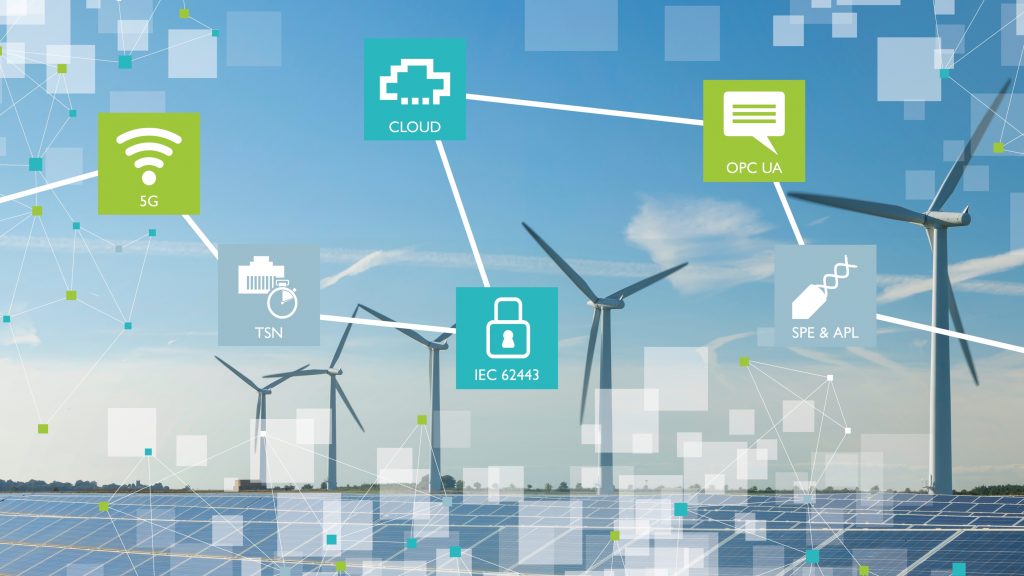
Interconnection of numerous electrolyzers to create gigawatt plants
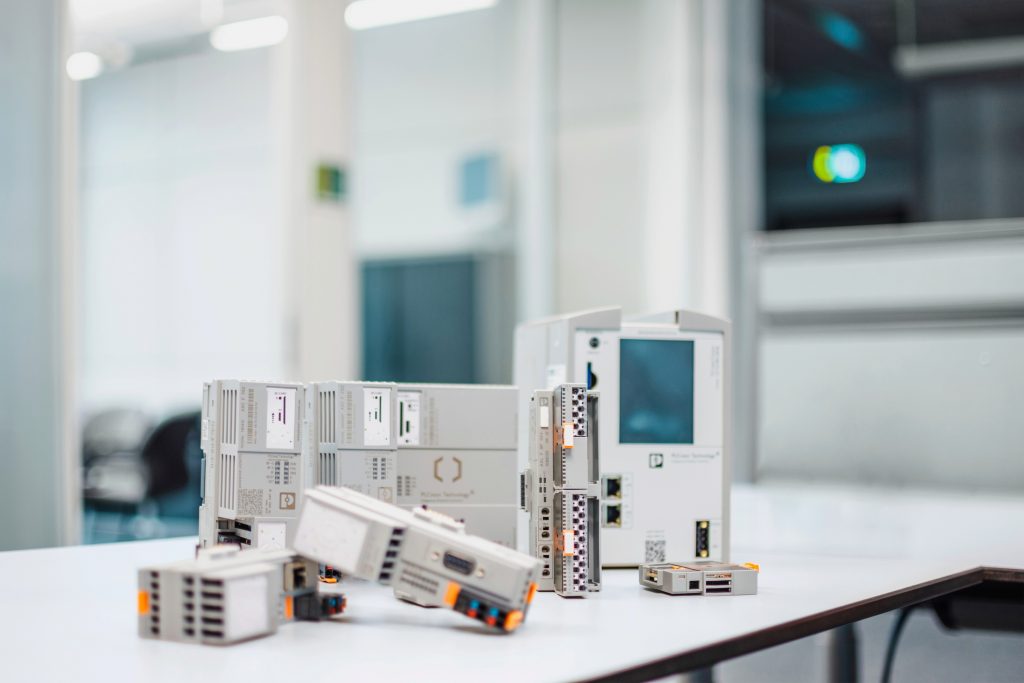
Germany is witnessing an increase in PtG plants, using various electrolysis methods and reaching several megawatts of power. Plans for 100 MW plants are underway in Lower Saxony. Projects in Neom and Rotterdam will utilize gigawatt-scale electrolyzers. Germany aims to create 10 GW of electrolysis capacity by 2030. Green hydrogen is converted back using fuel cells or chemically into substances like ammonia or methanol. Automation and communication strategies are crucial for all processes, from hydrogen generation to consumption.
Manufacturing containers based on the industrial model
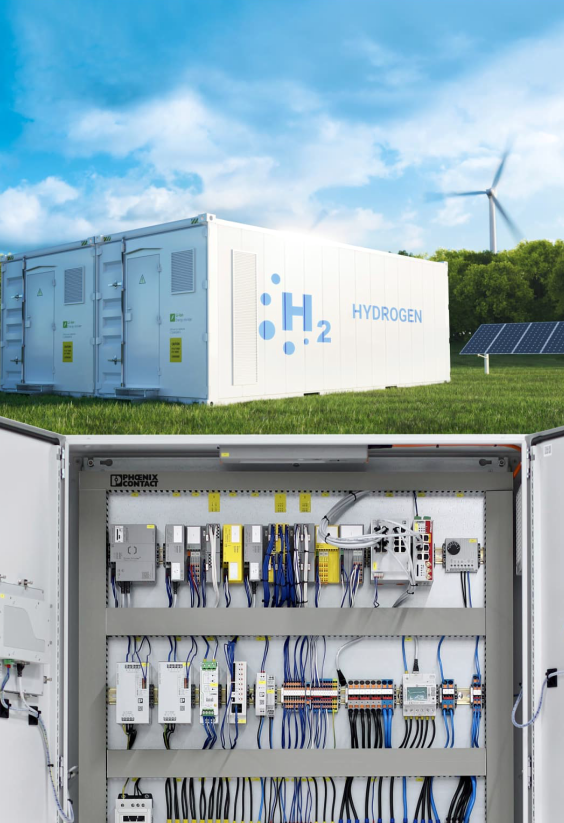
Manufacturers are developing containerized electrolyzers for hydrogen production, allowing for modular and interconnected gigawatt-scale plants. Industrial manufacturing methods enable efficient mass production of these containers. Providers like Phoenix Contact offer connection and automation technology, assisting with component selection and providing engineering and design services. Enapter AG’s AEM Multicore electrolyzer system uses an ion-conducting membrane and a cheaper catalyst, allowing for cost-effective hydrogen production with renewable electricity.
Supply of ready-to-use control cabinets based on PLCnext Technology
Enapter’s scalable AEM Multicore solution consists of interconnected stack modules in a container, producing up to 450 kg of hydrogen per day. Phoenix Contact provides control technology and DC power supply for the electrolysis stacks, including ready-to-use control cabinets. The container control room monitors hydrogen production, tank levels, and safety measures. Phoenix Contact’s PLCnext Technology handles control tasks and supports maintenance concepts. The control cabinets incorporate Ex protection components for hazardous areas.
Implementation of safety-related applications up to SIL 3
Phoenix Contact’s automation solution allows for safety-related applications up to SIL 3 in electrolysis plants. They offer cost-effective options, such as extending the PLCnext Control with an SIL 3 module. Their safety portfolio includes power supply units, relays, and motor starters. Comprehensive solutions for DC power electronics, like Charx Power modules, are available. The use of electrical connectors improves assembly efficiency and reduces costs. Phoenix Contact provides a wide range of products to support the scaling of hydrogen production in Germany.
Consultation in all phases of the lifecycle
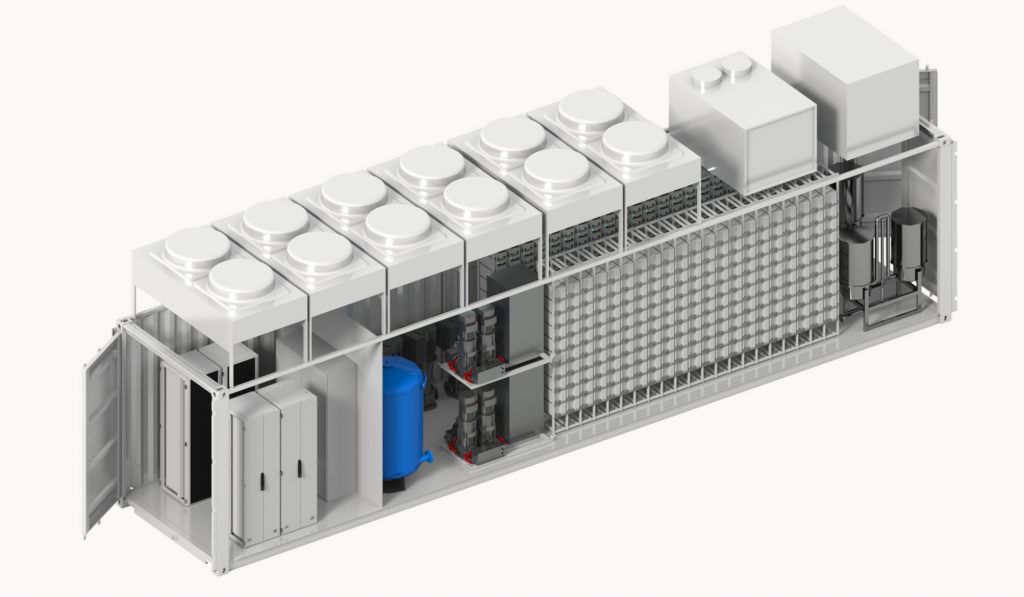
Phoenix Contact offers consultation services for various aspects of plant development. They help determine cooling capacity, assess safety integrity levels, and provide assistance with technical specifications, safety software implementation, and testing. Their consulting service covers control cabinet building, including CE marking, EMC, explosion protection, and access protection.
Communication solutions in all directions
Phoenix Contact supports communication and integration in power-to-X applications. They assist with the dynamic operation and functional integration of electrolyzers with power generation and consumption areas. They provide solutions for fuel cells as emergency power systems and offer support for remote control, maintenance, data collection, and digital twin implementation. Their portfolio includes products for reliable and secure data transmission. Phoenix Contact’s certified products ensure IT security. They are also developing software modules for future use, enabling newcomers to create their own software applications in the power-to-X industry.
MTP as the basis for modular solutions
Phoenix Contact supports the implementation of large modular electrolysis plants for green hydrogen production. They facilitate scalability and reduce implementation effort through the use of standardized MTP (Module Type Packages) interfaces, allowing for modular automation solutions.
Find out more about the new standards on our website.