Data-driven analysis options for the factory
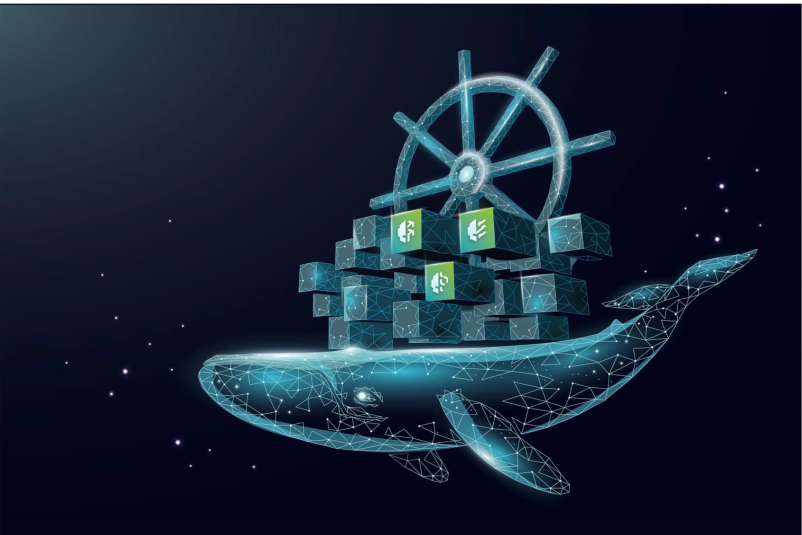
Data-driven analysis of production systems enables predictive insights for machine condition, energy use, and performance. Furthermore, As a part of the “Digital Factory now” concept, Phoenix Contact offers modular hardware and software solutions for independent data acquisition. Control cabinets like Data Collection Box and Secure Edge Box integrate with existing infrastructure, with adaptable source code. Moreover, open-source tools like Grafana, Node-RED, and InfluxDB enhance flexibility.
Creating, training, and executing machine-learning models with MLnext
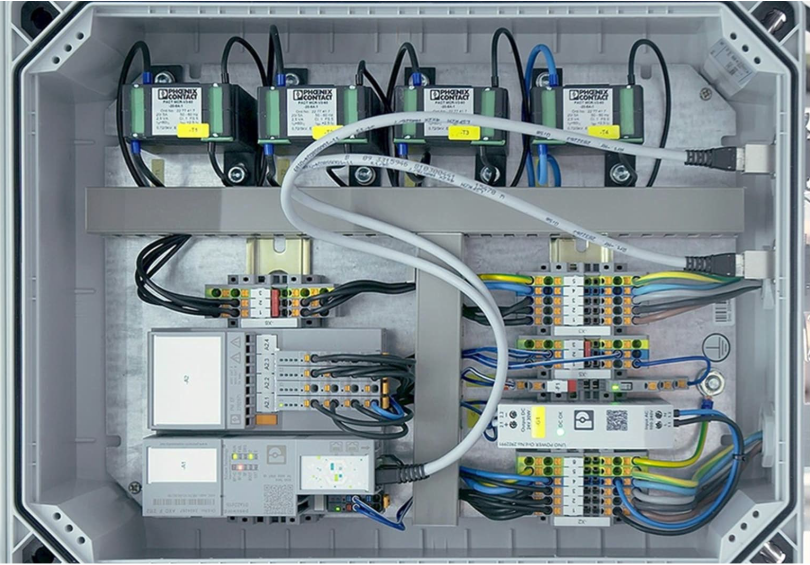
Once the data has been stored in a database, the user can use the MLnext software portfolio from Phoenix Contact to create, train, and execute machine-learning models. With the MLnext Framework, developers can evaluate time series data, while the MLnext Creation app offers ready-made templates for model creation and testing. The MLnext Execution app allows model creation without programming, supporting the entire application cycle for uncovering potentials and issues.
Planning needs-based maintenance measures
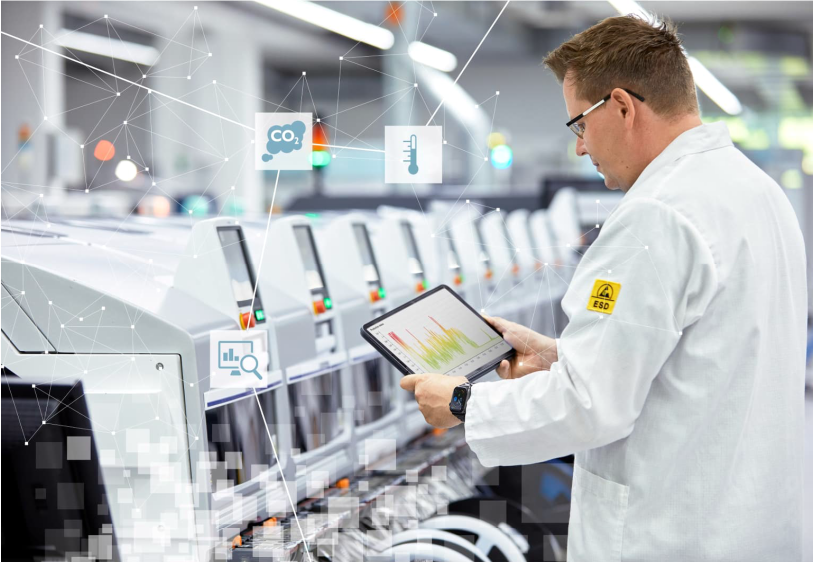
The condition-based maintenance system uses energy and process data to plan maintenance based on the condition of the system, creating a digital system representation. Furthermore, data is collected by the Data Collection Box, standardized, and sent to the Secure Edge Box. A time series database archives the data, which can be visualized via a web app. Users can then use MLnext Creation to build a machine-learning model for comparing normal behavior during production.
Visualization of the actual health, process, and consumption data
The created machine-learning model is stored and used for predictions. MLnext Execution on the Secure Edge Box evaluates system data in real time. If the model detects an anomaly, alarms are triggered via email or message. This proactive approach helps prevent downtime and enhances maintenance planning, ultimately increasing production availability.
Reducing or preventing system downtimes
At Phoenix Contact PLCnext Factory, a condition-based maintenance system monitors energy usage in production, tracing anomalies and reducing downtime. MLnext also analyzes critical supply units to prevent wear-related downtimes. The “Digital Factory now” concept predicts product quality and reduces rejects during restarts.
Find out more about Digital Factory with MORYX here.
Find out more on our website.