Less fossil-fuel energy and lower emissions
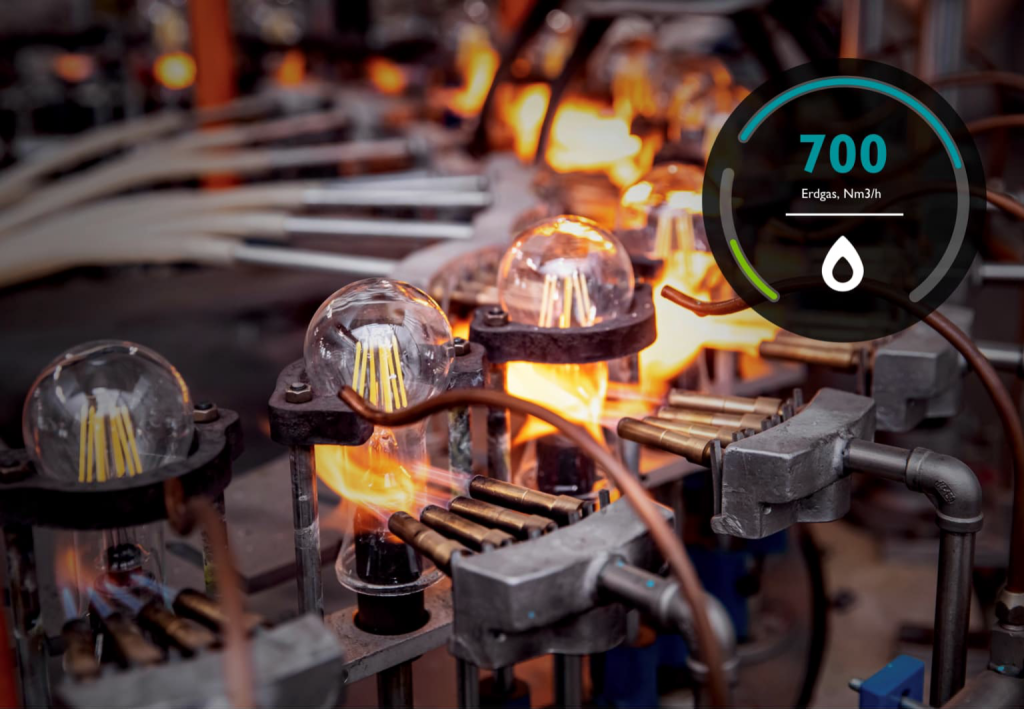
Phoenix Contact offers a solution for energy-intensive glass manufacturing to achieve Net Zero climate goals, using PLCnext Technology’s IIoT framework. An auxiliary heating system was integrated into a glass plant in Egypt in 2009 to enhance glass quality and reduce emissions. This decision now plays a crucial role in transforming the glass industry into sustainable factories amidst rapid changes driven by factors like climate change and digitalization.
Capturing all utilities efficiently, and intelligently, with minimal process interventions
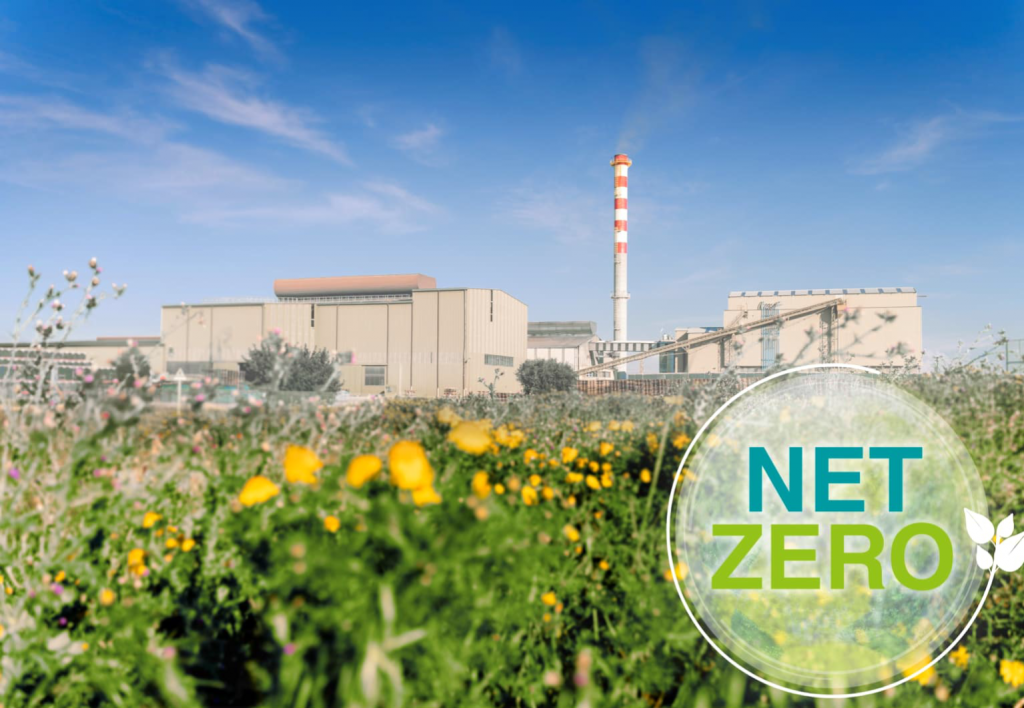
The “All Electric Society” envisions a world where renewable electrical energy is the main energy source, abundant, cost-effective, and environmentally friendly. Industries, like glass manufacturing, must adapt their processes across various areas, from raw materials to production, for sustainable climate strategies. Existing factories using different media face challenges, especially in optimizing fuel and water use efficiently and resourcefully. These improvements should be applied in both traditional and modern networked factory settings.
ML-supported process optimization with the PLCnext Technology
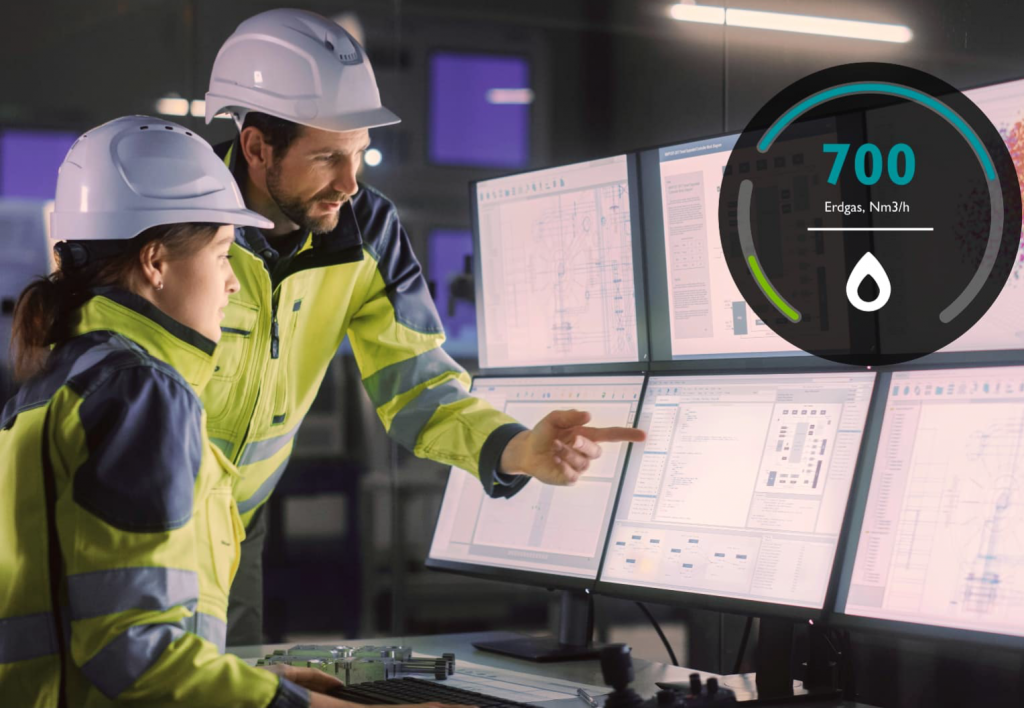
Early detection of anomalies in sensors and actuators along the glass manufacturing process brings several benefits. Firstly, it prevents disruptions, allowing for uninterrupted production. Secondly, it improves equipment efficiency, resulting in cost savings. Additionally, it optimizes fuel-air ratios and electrical heating, reducing energy consumption. Furthermore, it enables smart monitoring of various parameters for enhanced process control. To assist specialists in process optimization, Phoenix Contact offers MLnext, a machine learning system available on the PLCnext Store online marketplace. To ensure global accessibility, Phoenix Contact has introduced the Digital Factory Now initiative. This initiative provides open and standardized automation solutions based on PLCnext Technology. Consequently, it facilitates tailored solutions, from glass production to building-specific applications, in alignment with the goals of the All Electric Society.
International certification for safety and security
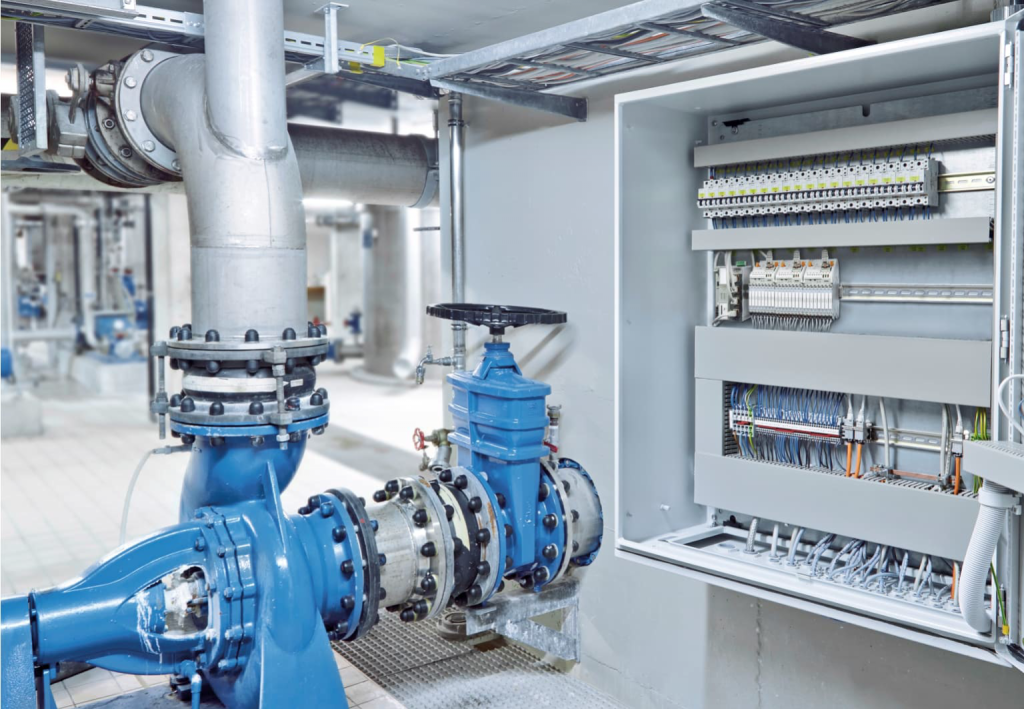
The OT Security certification of the PLCnext Control family by TÜV Süd, aligned with IEC 62443-4-2, along with existing safety certifications, establishes new industry standards. IEC 62443 is the primary global standard for OT security, while functional safety is defined by standards like IEC 61508, ISO 13849, and IEC 62061. Future automation solutions must bridge both perspectives. Due to the need for protection against tampering and remote access considerations, OT security is gaining prominence in the upcoming Machinery Directive. The certified PLCnext Control family already complies with the Machinery Directive requirements.
Field-side signal connection using smart signal conditioners
Users want to optimize fuel-to-air ratios securely using a parallel sensor system or their DCS. They aim to incorporate AI and implement a segmented network per IEC 62443. This is achievable by connecting signals through PLCnext Edge Devices or utility metering control cabinets, enabling real-time data exchange with IT/cloud, ERP/MES, or DCS systems. The glass industry can now advance sustainability and secure networking with these solutions.
Find out more about Digital Factory.