Masken Marke Eigenbau
Gleich zwei unserer Tochtergesellschaften haben in der Coronazeit außergewöhnliche Projekte auf die Beine gestellt, um Gesundheitssysteme und andere Einrichtungen mit sogenannten „Face Shields“ zu versorgen. Schnelles Handeln war hier gefragt! Alle Infos im neusten Blogbeitrag.
Die Pandemie hat auch unseren Alltag als Industrieunternehmen auf den Kopf gestellt. Wir haben uns vielen neuen Herausforderungen stellen müssen. In Blogbeiträgen aus verschiedenen Unternehmensbereichen zeigen wir euch, was wir dabei gelernt haben.
Auch in Polen stand das Gesundheitssystem im Frühling vor gewaltigen Herausforderungen. Wie überall gehören die Mitarbeitenden im Gesundheitssystem zu denen, die das höchste Risiko tragen, sich zu infizieren. Und wie überall war gerade am Anfange der Krise der Mangel an Schutzausrüstungen ein ernstes Problem. „Wir haben überlegt, wie wir helfen können“, berichtet Damian Bakowski, Abteilungsleiter für die Entwicklung und Einführung neuer Technologien am Phoenix Contact-Standort im polnischen Nowy Tomysl. Schnell kam sein Team auf die Idee, das eigene Know-how in der Kunststofftechnologie zu nutzen, um Visiere zu produzieren. Darin steckt allerdings auch ein Stück Herausforderung, handelt es sich aus Sicht der Fertigung doch um ein völlig neues Produkt. Von der Idee bis zum ersten fertigen Teil, das aus der Maschine fällt, vergehen normalerweise Monate.
3-D-Druck als schnelle Lösung
„So viel Zeit, das wussten wir, haben wir nicht. Uns war klar, hier geht es nicht einmal um Wochen, eher um Tage.“ Sie nahmen die Herausforderung an: „In der ersten Stufe haben wir auf die 3-D-Technik gesetzt.“ Dafür haben wir ein Visier konstruiert. „Wir begannen sofort mit der Produktion. Mit dieser schnellen Technik konnten wir zehn der Helme fertigen. Nicht viel, aber zu diesem Zeitpunkt dringend benötigt. Wir haben die sofort weitergereicht, überall dorthin, wo gerade der Bedarf am größten war.“
Dabei jedoch beließ man es nicht. „Während die Produktion auf den 3-D-Maschinen anlief, haben unsere Expertinnen und Expertene gleichzeitig die Werkzeuge konstruiert und gebaut.“ Die waren nach fünf Tagen fertig. Eine erstaunliche Leistung des Werkzeugbaus!
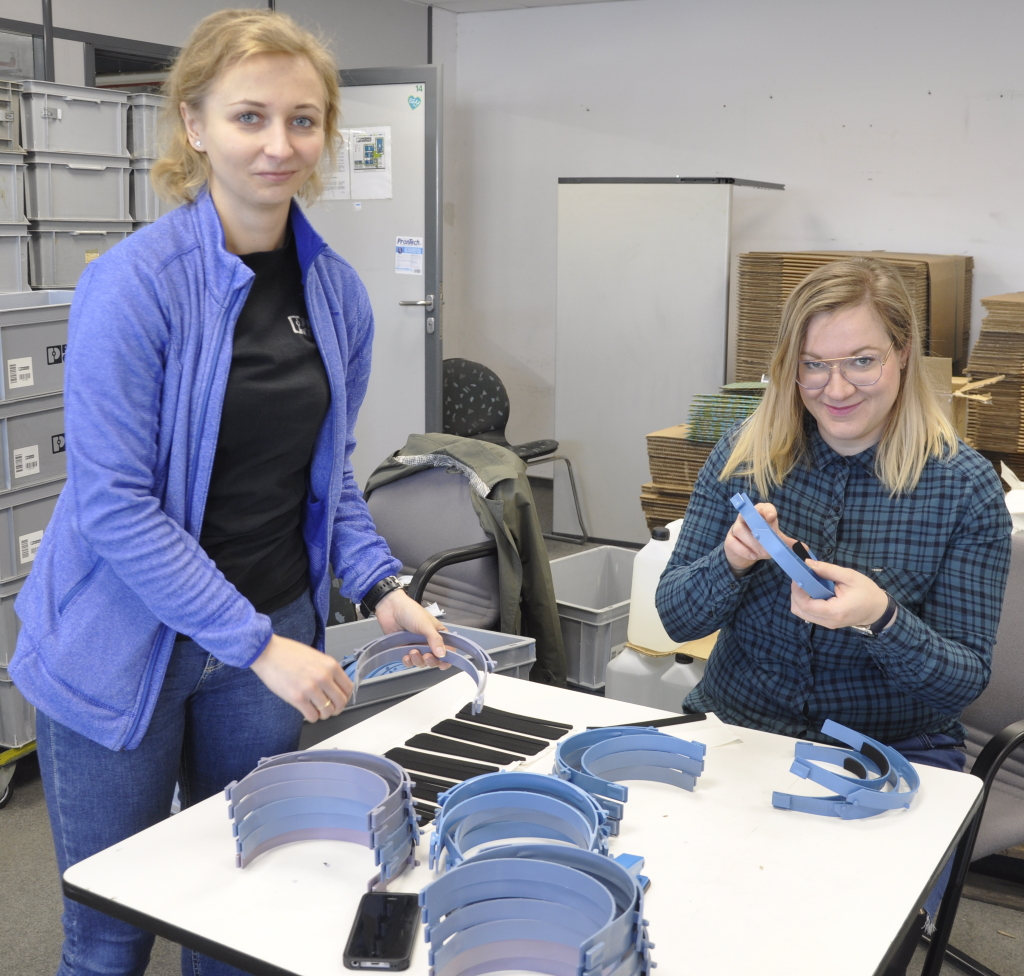
Wenn ein Werkzeug fertig ist, heißt das nicht, dass die Fertigung sofort starten kann. Es sind Serien von Testläufen und Anpassungen nötig. „Auch hier haben wir Gas gegeben. Schon nach weniger als zwei Wochen konnten wir die ersten 3.000 Visiere spenden. Insgesamt liegen wir inzwischen bei über 13.000.“ Zu den Visieren gehört auch eine einfache Kopfhalterung, ebenfalls in Polen konstruiert und gebaut. „Die Teile haben wir vor Ort in einer kleinen improvisierten Werkstatt montiert.“
Systemrelevante Einrichtungen unterstützt
Die fertigen Schilde gingen nicht nur an Gesundheitseinrichtungen: „Wir haben zum Beispiel ebenfalls die Polizei und die Feuerwehr beliefert. Auch die Mitarbeitenden und Freiwilligen dort sind schließlich nicht nur wichtig, sondern auch hochgradig gefährdet.“ Den Kreis der Einrichtungen konnten wir durch die hohe Produktionsleistung inzwischen erweitern: „Wir spenden nun auch an Kindergärten und ähnliche Einrichtungen.“
Zusätzlich wurde eine weitere Spendenaktion gestartet: „Wer möchte, kann die Schilde kaufen, um sie zum Beispiel an Verwandte und Freunde weiterzureichen. Den Erlös spenden wir den Krankenhäusern an unseren beiden Produktionsstandorten in Nowy Tomysl und Tarnobrzek.“
Die Aktion hat sich für alle gelohnt, wie Magda Pawinska aus der Kommunkationsabteilung berichtet: „Wir haben nicht nur oft ein herzliches Danke gehört, sondern in diesen schwierigen Zeiten manches Lächeln auf sonst sorgenvolle Gesichter gezaubert.“
Verlängerte Werkbank der Uni
Etwas kleiner im Maßstab, aber gemessen an den Möglichkeiten vor Ort auch eine erstaunliche Leistung: Unsere amerikanische Tochtergesellschaft in Harrisburg hat in einem außergewöhnlichen Projekt bisher über 200 dieser Schutzeinrichtungen für Mitarbeitende im Gesundheitswesen von Harrisburg und Umgebung produziert.
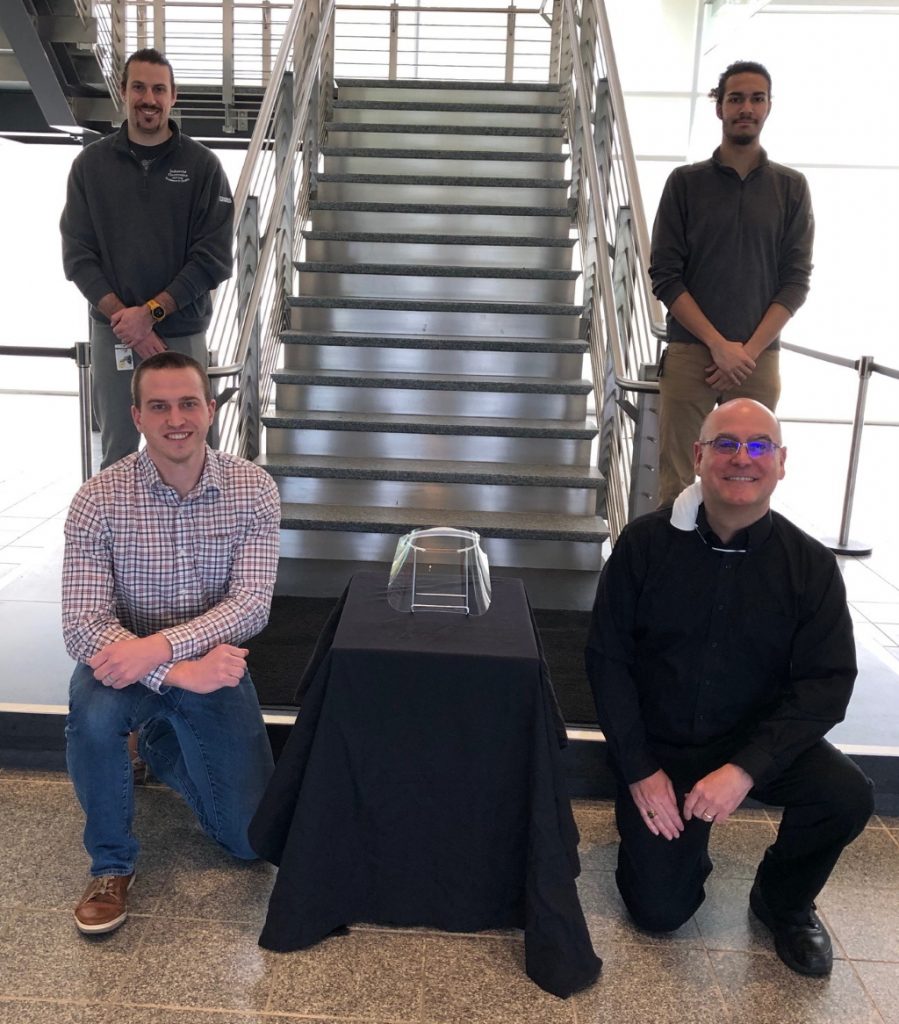
Molly McGowan, die Kommunikationsexpertin in den USA, berichtet: „Auf dem Höhepunkt der Krise in den USA wurde wie in vielen Ländern auch bei uns die Schutzsausrüstung knapp.“ Viele überlegten, wie man helfen kann. „Anfang April sah der Produktionsingenieur Josh Frey den Bericht eines regionalen Fernsehsenders. Studierende an der Universität Harrisburg bauten Schildmasken für Mitarbeitende in den Gesundheitseinrichtungen. Dafür nutzten sie die 3-D-Drucker der Uni. Er dachte sich: „Solch ein Gerät haben wir doch auch.“ Frey setzte sich mit dem Experten Brent Balmer zusammen. Der rechnete und kam zum Schluss: „Ja, das können wir auch.“ Die Daten aus den Maschinen der Uni konnten wir auf der Anlage in unserer Tochtergesellschaft übernehmen. „Wir waren so etwas wie eine verlängerte Werkbank und konnten so die Kapazitäten der Uni erweitern.“ Rechtlich kein Problem, da die Konstruktionsdetails „Open Source“ sind, also für jedermann kostenlos zur Verfügung stehen.
Vor Ort montieren die Studierenden die transparenten Schilder auf die Kopfhalterungen zu fertigen Masken. Die gehen dann an die lokale Gesundheitsbehörde.

Facebook, Instagram, Snapchat, TikTok – ohne die sozialen Medien geht heutzutage gar nichts mehr. Ich liebe es, auf den verschiedenen Kanälen unterwegs zu sein und mir Informationen und Inspirationen zu holen. Selbst schreibe ich gerne alles, was kein Literaturverzeichnis braucht. Außerhalb des Internets trifft man mich am ehesten beim Sport. Besucht mich auf LinkedIn.
0 Kommentare