Löten oder löten lassen? Einem Roboter das Löten beibringen
Eine Kiste voll mit ca. 40.000 LEDs, eine verrückte Idee, ein bisschen Zeit und die Suche nach dem richtigen Werkzeug: So entstand im Ausbildungszentrum von Phoenix Contact in Schieder ein Lötroboter. Diese Geschichte zeigt, wie man technische Probleme mit Erfindergeist und einer Menge Know-how löst und dabei auf topmodernes Equipment zurückgreifen kann.
„Niemand wusste, wofür die LEDs sein sollten. Die Kiste lag schon eine ganze Weile bei uns im Labor herum“, erinnert sich Anton Krusenotto. Der 19-Jährige hat 2021 bei Phoenix Contact als dualer Student begonnen, Fachrichtung Elektrotechnik. Gerade macht er noch die parallele Ausbildung zum Elektroniker für Geräte und Systeme. Seit diesem Monat sitzt er immer wieder im Hörsaal an der Hochschule OWL in Lemgo.
Geschätzt rund 40.000 einzelne Durchsteck-LEDs waren in der Kiste. „Dann hatte ich mit den Kollegen die Idee, dass man daraus ein LED-Display bauen könnte.“ Gesagt, getan. Rund 8.000 LEDs waren dafür veranschlagt. Eine Leiterplatte musste her, um die LEDs zu platzieren, bestromen und steuern zu können. „Die habe ich dann entwickelt“, erklärt Anton Krusenotto. Die Anzahl der LEDs machte ihre manuelle Verarbeitung auf den Leiterplatten schier unmöglich. 8.000 LEDs bedeuten bei zwei Kontakten pro LED insgesamt rund 16.000 Lötpunkte. Das von Hand machen – unmöglich.
Zumal Anton Krusenotto sich dieses Projekt „so nebenher“ vorgenommen hatte: Sein Teil einer Projektarbeit im Rahmen seiner betrieblichen Ausbildung war erfolgreich erledigt – etwas schneller als gedacht. Er suchte nun nach weiteren Herausforderungen. Genau für solche Vorhaben ist das Ausbildungslabor in Schieder der richtige „Spielplatz“.
Auch sein Ausbilder Daniel Bäckeralf war sofort begeistert: „Ich unterstütze das immer gern, wenn jemand eine Idee für Sachen hat, die wir hier sonst nicht so einsetzen.“ Der Roboter diente bisher eher als Ausbildungsstation für das Thema Programmieren und Steuern. Ungewöhnliche Umbauten, wie sie Anton Krusenotto vornehmen wollte, gab es bisher selten. „Wenn jemand eine Idee hat, wie der Roboter noch eingesetzt werden kann und er wird sonst gerade nicht genutzt. Warum nicht?!“
Gesucht: das richtige Tool
Die Lösung für das Lötproblem stand also bereits im Raum. Sie heißt Epson S5, hat sechs Achsen, einen Arm und macht nur das, was man sagt. Besser, was man einprogrammiert. Der hochmoderne Industrieroboter ist Equipment des Ausbildungslabors in Schieder, fester Unterrichtsbestandteil der Elektronikerausbildung und arbeitet so auch an den Fertigungsstandorten von Phoenix Contact.
„Weil es so viele LEDs sind, habe ich gedacht, dass man das den Roboter machen lassen kann“, erinnert sich Anton Krusenotto. „Der war damals gerade nicht im Einsatz und frei“, ergänzt Ausbilder Daniel Bäckeralf. Er half dem Studenten bei seinem ambitionierten Projekt, das von der Ausgangsidee plötzlich auf eine ganz andere Spur kam.
Denn es ging jetzt nicht mehr in erster Linie darum, eine LED-Video-Wall zu bauen, sondern die LEDs auf die Leiterplatte zu bekommen. Der weiße Industrieroboter versprach die Lösung. Was könnte besser geeignet sein als ein Roboterarm. „Wir hatten plötzlich ein Werkzeug gefunden, mit dem wir uns viel Arbeit ersparen konnten“. Der Roboter war ja schon vorhanden.
Aber das war nur die „halbe Miete“. Anton Krusenotto: „Dann habe ich eine Halterung in 3-D gedruckt, die man an die Werkzeugplatte des Roboterarms schrauben konnte. Da ließ sich der Lötkolben befestigen.“ Aber auch damit ist das System noch nicht fertig. Wer löten will, braucht Lötzinn.

Alles andere als trivial
„Ich habe eine Zuführung mit einem Motor entwickelt, der das Material durch ein Röhrchen führt,“ erklärt Anton Krusenotto. Dann das Ganze befestigen, verdrahten, elektrifizieren, ansteuern. „Es war eine ziemliche Herausforderung, die Steuerung des Lötkolbens mit dem Roboter zu verbinden,“ erinnert sich der Student. Und dann kam etwas, das jeder kennt, der selbst mal den Lötkolben in die Hand genommen hat: Die Spitze verschmutzt irgendwann und dann geht gar nichts mehr.
Ausbilder Daniel Bäckeralf weiß: „Das ist nicht so trivial. Man muss die Spitze sauber halten, damit die Lötstelle sauber ausgeführt wird und keine Flussmittelreste übrig bleiben. Dann muss die Position passen. Es muss natürlich der Zeitpunkt passen, wann das Zinn zugeführt wird. Es muss abgestimmt sein, wie viel zugeführt wird.“
„Am Anfang hatte ich die Lötkolbenreinigung gar nicht bedacht“, sagt Anton Krusenotto, „ich habe dann bemerkt, dass der Kolben richtig dreckig wird.“ Aber auch dafür war schnell eine Lösung gefunden: Bei einer manuellen Lötstation im Labor war ein Reinigungsgerät, zwei gegeneinander rotierende Schwämme mit elektronischer Regelung, die er kurzerhand auf die Montageplatte des Systems befestigte. „In diese Station habe ich den Lötkolben immer wieder reinfahren lassen. Damit habe ich das Problem behoben.“
Die Arbeit geht weiter
Der Rest war vor allem Probierarbeit, um die ideale Kombination des Ablaufs zu finden. Das Ganze musste dann „nur noch“ in das Programm zur Steuerung des Roboters überführt werden. Knifflig war, den zusätzlichen Motor der Lötzinnzuführung mit der Hauptsteuerung des Roboters zu verknüpfen. Aber auch das ließ sich mit hauseigener Technik von Phoenix Contact und Erfindergeist lösen.
Der Roboter ist inzwischen in seinen Werkszustand zurückversetzt. Er wartet auf die nächsten Auszubildenden in der Ausbildungswerkstatt. Die LEDs sind nicht viel weniger geworden, weil sich sehr schnell herausgestellt hat, dass die geringen Pinabstände, die für die Mini-LEDs notwendig wären, sich mit einem solchen Roboterarm nicht exakt löten lassen. Anton Krusenotto: „Leider ist der Roboter nicht genau genug, um die kleinen LEDs zu verlöten.“
Aus der Video-Wall ist damit bisher noch nichts geworden. Aber das Projekt „Lötroboter“ hat Anton Krusenotto natürlich dennoch zu Ende gebracht. Mit dem Ergebnis ist er sehr zufrieden: „Ich habe einige Testplatinen mit größerem PIN-Abstand gemacht und verlötet. Die hat der Roboter echt gut gemacht.“
Mehr über Projekte von unseren Auszubildenden und dual Studierenden lest ihr hier:
Klemme trifft Turnschuh: Austauschprojekt mit Adidas
Als Botschafter unterwegs
Hey, Emma! – Ein Gebäude lernt sprechen
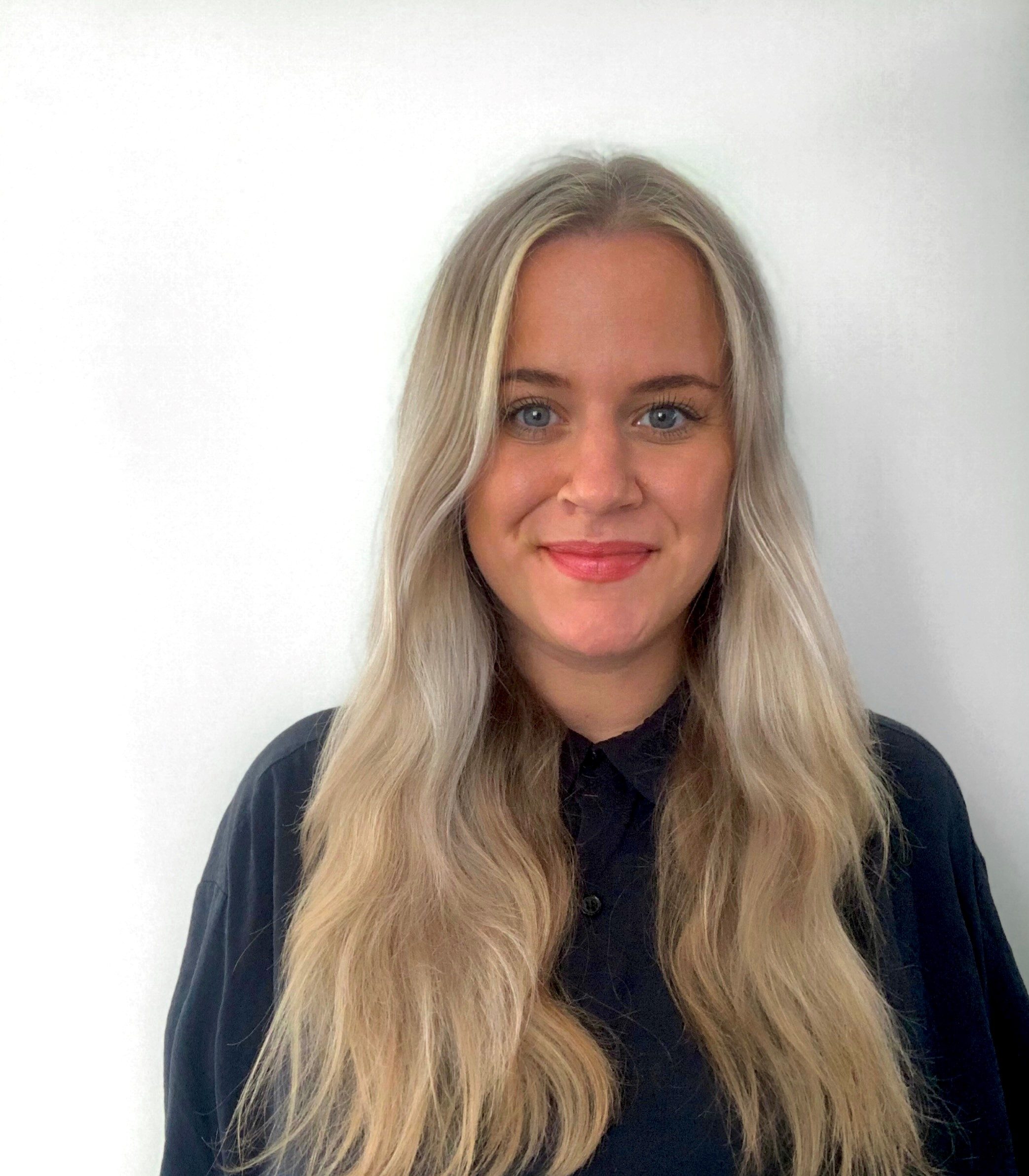
Als Digital Native sind Social Media und Blogs aus meinen Leben kaum wegzudenken. Ich bin ein großer Fan sozialer Netzwerke, da Kreativität, Networking und Inspiration an erster Stelle stehen. Neue Kulturen und die schönen Ecken der Welt lerne ich aber lieber analog kennen – auch in Form von Wochenendtrips. Besucht mich gern auf LinkedIn oder Xing.
1 Kommentare
Antworten
Habe gleich 5 Sterne dagelassen;)
LG
Ludwig