Höllenfahrt für Lithium-Ionen-Akkus
Die Welle der E-Mobilität kommt. Und zwar gewaltig. Damit verbunden ist die Entwicklung und Erprobung neuer Technologien in bisher ungeahnten Dimensionen. Bei Phoenix Testlab in Blomberg werden bis zu 800 kg schwere Lithium-Ionen-Akkupakete getestet (kurz: Li-Ion-Akkus). Ein Blick hinter die Kulissen einer modernen Folterkammer: ins Batterielabor.
Ein Airbag, der auslöst, wenn man das Radio einschaltet? Klingt gefährlich. Damit genau so etwas nicht passiert, prüft Phoenix Testlab die Produkte von morgen und zertifiziert sie für ihre Hersteller. Was man da prüfen kann und wie solche Prüfungen durchgeführt werden, erzählen wir euch in unserer Phoenix Testlab-Reihe.
Das Thema ist sprichwörtlich heiß: Immer wieder geistern Nachrichten von brennenden E-Autos durch die Nachrichten. Das Thema Akkumulator bekommt durch die enorme Energiedichte und ihren Einsatz im rollenden Alltag eine ganz neue Brisanz. Und damit auch Dinge wie Haltbarkeit, Dauerbelastung und Sicherheit. Daher ist Phoenix Testlab in Blomberg bei der Automobilindustrie eine allererste Adresse.
„Wir machen Akkus alt. Und das ganz schnell.“ Der, der das sagt, trägt keinen Zauberhut oder ist im Besitz einer Zeitmaschine. Michael Jonca leitet das Batterielabor bei Phoenix Testlab. Und wirkt nicht nur ausgesprochen sympathisch, sondern auch sehr seriös. Also kein Hokuspokus, sondern echte technologische Pionierleistung, mit der den Energiespendern von E-Fahrzeugen hier zu Leibe gerückt wird.
Die Herren der Zeitreise
„Unsere Aufgabe ist es, Li-Ion-Akkus künstlich altern zu lassen. Durch unsere ausgeklügelten Testverfahren stressen wir die empfindlichen Energieträger so, dass dies weit mehr als einem Autoleben entspricht.“ Eine virtuelle Zeitmaschine. Also doch! „Dabei richten wir uns streng nach den Vorgaben der Hersteller“, erklärt Michael Jonca seine Aufgaben.
Phoenix Testlab ist ein unabhängiges Prüfinstitut, welches 1994 von der Phoenix Contact GmbH & Co. KG gegründet wurde – damals noch unter dem Namen Phoenix EMV-Test GmbH. Anlass war die seit dieser Zeit vorgeschriebene Elektromagnetische-Verträglichkeits-Prüfung (kurz EMV). Mehr zur Gründung von Phoenix Testlab lest ihr hier. Von Beginn an war die Unabhängigkeit des Instituts trotz der räumlichen Nähe zum gründenden Unternehmen ein wichtiges Merkmal des Testlabors. Diese Unabhängigkeit ist einer der Eckpfeiler für den raschen Erfolg des Hightech-Unternehmens. Ein anderer: Der Kunde ist König.

Daher gelten in den heiligen Hallen von Phoenix Testlab auch teils strenge Vorgaben der Kunden. „Sorry, aber diese Geräte und Prüflinge sind für Fotografen tabu.“ Das betrifft insbesondere die Automobilbranche. Für die und ihre bis zu 800 Kilogramm schweren Energiespeicher ist Phoenix Testlab seit 2011 ein nahezu unverzichtbarer Partner. Im Frühjahr dieses Jahres begann der Betrieb eines der modernsten Labore für die Prüfung von Lithium-Ionen-Batterien und -Modulen mit einer Größe von circa 950 Quadratmetern. Im Batterielabor testet Michael Jonca mit seinen Kollegen Prototypen vor der Serienfertigung. Die hier getesteten Batterien sind also die Grundlage für die später in Serie hergestellten Batterien im E-Auto.
„Der Aufbau dieses Testcenters begann mit diesen Containern.“ Zusammen mit Thomas Worsch, dem Marketingexperten von Phoenix Testlab, beginnen wir einen Rundgang durch das Prüfinstitut. „Container sind ideal, weil wir die jeweiligen Testkomplexe und die Prüflinge aus Sicherheitsgründen einzeln handhaben können.“ Michael Jonca führt aus: „Zwar testen wir hier keine Zerstörungsszenarien, setzen also den Prüfling nicht absichtlich der Zerstörung aus. Aber auch unsere Haltbarkeits- und Lebensdauertests stressen die großen Batterien erheblich. Daher gibt es auch eine ganz enge Zusammenarbeit mit der ansässigen Feuerwehr, die einen potenziellen Brand ohne Gefährdung des restlichen Testlab und der Mitarbeiter und umliegender Anwohner schnell unter Kontrolle bringen muss.“
In der Folterkammer
Die großen Batterieblöcke werden über Monate hart rangenommen. Erste Station ist die elektrische Prüfanlage. „Wir laden hier mit richtig Energie, boosten in ein bis zwei Stunden auf Vollladung. Und das viele tausend Male. Unser Stromverbrauch ist daher ähnlich hoch wie in der gesamten Fertigung von Phoenix Contact.“ Kein Wunder, dass am Ende dieses Testlaufs die Prüflinge ein bis zwei Wochen liegen gelassen werden, bis sie wieder an den Auftraggeber zurückgesandt werden. „Die chemischen Reaktionen im Akku sind ja nicht abrupt beendet, das klingt noch eine Weile nach“, erklärt der Chef vom Batterielabor. „Die Gefahr einer Entzündung auf dem Transportweg wäre zu hoch für eine sofortige Rücksendung.“
Um dann zur nächsten Folterkammer zu marschieren. Es wird mechanisch und hört sich nach Jahrmarkt an: „Das ist unser Shaker, unsere Rüttelkammer. Hier schütteln wir das Batteriepack rund zwei Wochen lang ununterbrochen, und das kombiniert mit einer Klimakammer, sodass wir hier Hitze und Kälte simulieren können.“ Die Ausmaße des haushohen Prüfstands sind enorm. „Wir heben den Prüfling mitsamt seinem von uns angefertigten Aggregatrahmen mit einem 5-Tonnen-Kran auf seinen Platz. Die stählerne Schüttelplatte wiegt allein 35 Tonnen. Sie ist im Fundament federnd gelagert, sonst würde im weiten Umkreis die Erde beben“, berichtet Thomas Worsch. Jonca ergänzt: „Hier testen wir auch Komponenten aus der Schifffahrt und Industrie, nicht nur Batterien, sondern auch ganze Schaltschränke. Und die können bis zu vier Tonnen wiegen.“ Der Prüfstand rüttelt im „einaxialen Schwingungsverfahren“. Um einen Prüfling in allen drei Dimensionen durchzuschütteln, wird seine Lage auf der Prüfanlage verändert. Eine Gemeinheit hat der Prüfstand aber noch drauf: „Wir simulieren hier auch einen mechanischen Schock, also etwa die Fahrt über einen Bordstein. Da lasten dann bis zu 50g (g für Gravität, hier das 50-fache der Erdbeschleunigung) auf dem Prüfling.“
Die Batterien sind je nach Kundenwunsch mal sechs Monate, mal fast anderthalb Jahre bei Phoenix Testlab. Nicht herum kommen die bemitleidenswerten Dauerläufer um das nächste Testmartyrium: den T-Schocker. „Zehn bis dreißig Tage lang muss der Batteriepack einen Temperatursturz von -40 °Celsius bis +75° Celsius aushalten – im ständigen Wechsel. Das sind ganz typische Anforderungen aus der Automobilindustrie“, lässt uns Michael Jonca staunen. „Dabei geht es ebenfalls um die mechanische Festigkeit. Denn hier wird die Dichtigkeit der Außenhülle strapaziert.“
Letzte Hürde Schwimmbad
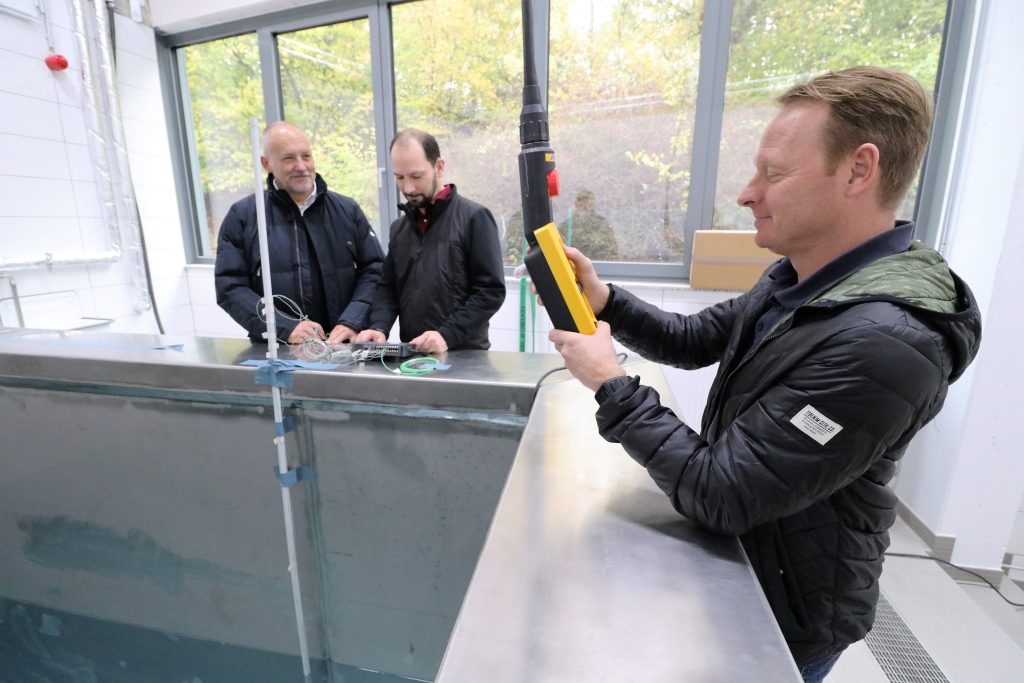
Ist der Prüfling bis hierhin noch immer bei guter Laune, droht ihm im Tauchbecken die nächste Tortur. „Dieses große Becken ist ganz neu“, hallt Joncas Stimme durch das ganz spezielle Schwimmbad. An der Decke der große Kran, der die Batterien ins kalte oder warme Wasser hebt. „Wir können das Wasser auch beheizen.“
Für jedes Akkupaket ist ein Team an Ingenieuren und Mitarbeitern zuständig, denn die jeweiligen Testprozeduren sind komplett unterschiedlich. „Momentan befinden sich zwölf verschiedene Prüflinge und damit auch zwölf verschiedene Energieträger für ihre jeweiligen E-Fahrzeuge bei uns im Test.“ Wer den netten Herrn Jonca durch seine Folterkammern begleitet, der kann sich mit Sicherheit darauf verlassen, dass die Prüflinge, die dem Batterielabor heil entkommen, nahezu jede Tortur mit Leichtigkeit ertragen.
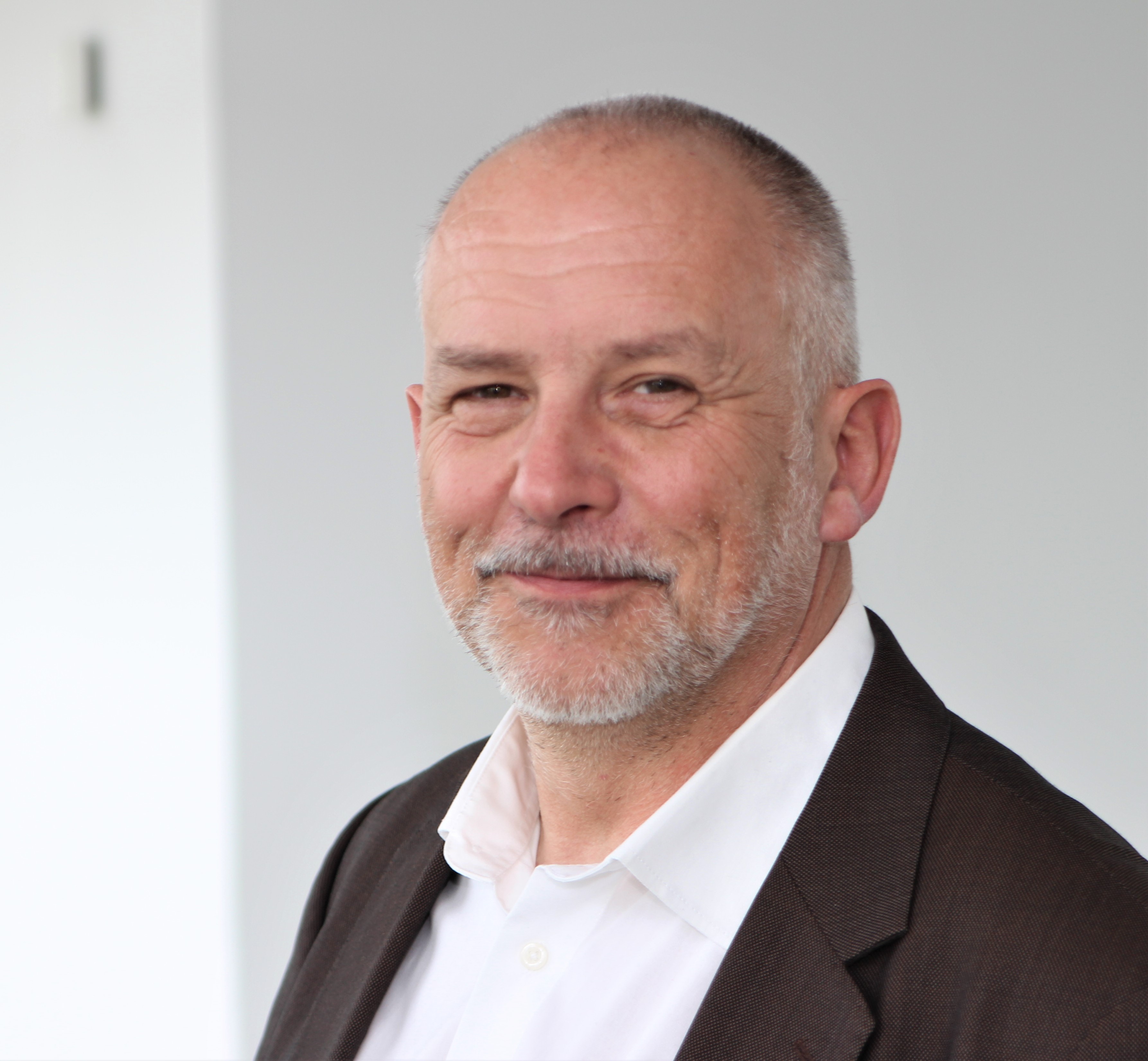
Mein Baujahr liegt schon länger zurück, nichtsdestotrotz tummele ich mich seit den Anfangszeiten digitaler Medien in selbigen. Als Journalist bin ich seit vielen Jahren mit dem geschriebenen Wort genauso per Du wie mit Video und Audio. Publizieren macht Spaß, also schreibe ich auch privat in zwei Blogs über meine Hobbys, netzwerke in Facebook, Instagram und Co. und moderiere YouTube-Videos. Eines meiner Hobbys ist orange und steht auf dem Parkplatz, für ein anderes hüpfe ich durch zugige Sporthallen. Einfach googeln, Ihr findet mich. Oder ihr besucht mich direkt auf LinkedIn.
0 Kommentare