Beraten, prüfen, zertifizieren: alles aus einer Hand
Wenn es um die Zukunft der Mobilität geht, sind die Batterien und ihre Leistungsfähigkeit ein entscheidender Faktor. Klar, dass daher die Prototypen auf Herz und Nieren geprüft werden müssen. Michael Jonca ist bei Phoenix Testlab Section Manager für die Laborbereiche Vibration, Acoustic & Battery und war stark bei der Konzeption und Ausrichtung der neuen Labore beteiligt. Heute spricht er mit uns über seine spannende Arbeit.
Ein Airbag, der auslöst, wenn man das Radio einschaltet? Klingt gefährlich. Damit genau so etwas nicht passiert, prüft Phoenix Testlab die Produkte von morgen und zertifiziert sie für ihre Hersteller. Was man da prüfen kann und wie solche Prüfungen durchgeführt werden, erzählen wir euch in unserer Phoenix Testlab-Reihe.
Ich habe Elektrotechnik in Kiel studiert und Phoenix Contact durch meine Diplomarbeit kennengelernt. Während meiner Diplomarbeit hatte ich ständigen Kontakt zum Unternehmen Phoenix Contact und konnte mich von der professionellen Vorgehensweise und dem familiären Arbeitsklima überzeugen. Nach meinem Studium bin ich direkt beim Schwesterunternehmen Phoenix Testlab als Prüfingenieur eingestiegen.
Gleich zwei neue Laborgebäude hat Phoenix Testlab im letzten Jahr gebaut. Eines für Umweltsimulation, EMV und Funkprüfungen und eines für reine Batterietests. Beide Gebäude sind dafür ausgerichtet, die hohe Nachfrage im Bereich der Elektromobilität zu bedienen.
In unseren Laboren prüfen wir im Bereich der Umweltsimulation, der elektromagnetischen Verträglichkeit (EMV), der elektrischen Sicherheit und vielem mehr. Seit einigen Jahren leite ich nun bei uns im Umweltsimulationslabor die Prüfungen in den Bereichen Akustik, Vibration und Batterie. Wenn wir von „Batterie“ reden, meinen wir damit die wirklich großen Batterien für Elektroautos, also in der Regel Lithium-Ionen-Batterien.
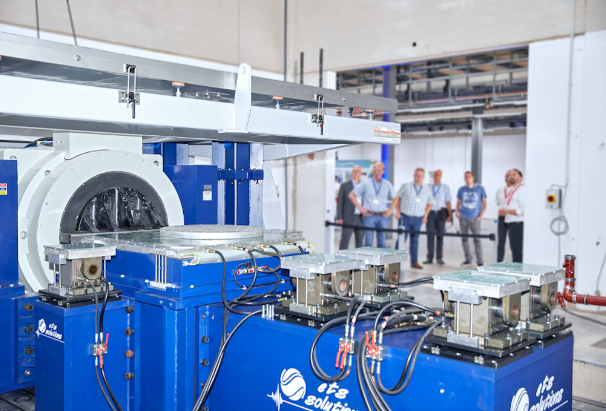
Strenge Anforderungen prüfen
Wir kommen in der Regel dann ins Spiel, sobald der Hersteller von Batterien Tests an verschiedensten Musterständen benötigt. Dadurch wird abgesichert, dass die Batterie später im Fahrzeug die hohen Anforderungen erfüllen kann. Damit das Produkt verkauft werden darf, benötigt der Hersteller zusätzlich einen Nachweis, dass alle gesetzlichen Vorschriften oder Standards erfüllt werden. Eine Automobilkomponente darf zum Beispiel keine anderen Geräte unverhältnismäßig stören, muss Temperaturschwankungen und Vibrationen aushalten und noch vieles mehr. Die Hersteller stellen deshalb strenge Anforderungen an die einzelnen Komponenten.
Shake it
Bei uns im Umweltsimulationslabor führen wir unter anderem Schwingungsversuche durch. Hier prüfen wir, ob das Produkt bei diesem Test mechanisch kaputt geht. Jeder, der schon einmal mit der Eisenbahn gefahren ist, weiß was es heißt, solchen Schwingungen ausgesetzt zu sein. Für die Versuche verwenden wir große Maschinen, die sogenannten Shaker. Diese sind sehr stark und funktionieren – vereinfacht ausgedrückt – wie ein riesiger Lautsprecher. Durch Strom wird eine Spule zur Schwingung angeregt. Diese wird dann auf den Prüfling übertragen. Besonders interessant dabei ist, dass wir Geräte aus den verschiedensten Bereichen prüfen. Hierzu zählen Produkte, die ihren Einsatz in der Industrie, im Auto, auf dem Schiff, in der Bahn oder in der Luft- und Raumfahrttechnik finden. All diese elektrischen Produkte müssen den neuesten Normen und Richtlinien entsprechen, da sie sonst nicht verkauft werden dürfen.
Der Zeit voraus
Das Tolle an meinem Job ist, dass wir viele Produkte testen, die erst in ein paar Wochen oder Monaten auf den Markt kommen. Wer bei uns arbeitet, kann deshalb schon einen kleinen Blick in die Zukunft werfen. Monotonie ist bei uns ebenfalls ein Fremdwort – da wir mit vielen Prototypen aus unterschiedlichen Bereichen zu tun haben, müssen wir jede Prüfung optimal auf den Prüfling abstimmen. Manchmal sind die Technologien selbst noch so neu, dass wir erst einmal mit den Herstellern Pionierarbeit leisten müssen, weil einfach noch zu wenig Normen und Richtlinien existieren. Das war zum Beispiel im Bereich der Batterieprüfungen der Fall: als wir vor 15 Jahren damit begonnen haben, war das eine völlig neue Technologie. In intensiver Zusammenarbeit mit unseren Kunden haben wir die Prüfungen seither stetig weiterentwickelt, neue Maschinen angeschafft und ein umfangreiches Sicherheitskonzept ausgearbeitet.
Viele Jahre war ich als Prüfingenieur beschäftigt und habe selbst eine Fülle von Umweltsimulationsprüfungen durchgeführt. Insbesondere habe ich mich um die Schwingungsversuche, Akustikprüfungen und Elektromobilität und die dafür benötigten Batterien gekümmert. Mittlerweile bin ich als Section Manager für diesen Bereich in unserem Labor zuständig und führe mit meinem Team die Prüfungen durch.
Durch den Neubau der beiden Laborgebäude haben wir unser Angebot nochmal deutlich erweitert. Beide Gebäude mussten zudem mit neuen Prüfressourcen aufgerüstet werden – so haben wir jetzt z.B. einen nagelneuen 300 kN-Shaker, mit dem wir auch die ganz großen Batterien für SUVs testen können. Ein zweiter Shaker wird derzeit aufgebaut. Phoenix Testlab steht für eine stetige Weiterentwicklung der Prüfmöglichkeiten und der Prüftechnologien. Dies tun wir, um den Anfragen unserer Kunden gerecht zu werden und Phoenix Testlab für die Zukunft auszurichten.
Einen weiteren Bericht aus unserem Batterielabor folgt nächste Woche. Abonniert unseren Newsletter, um ihn nicht zu verpassen!
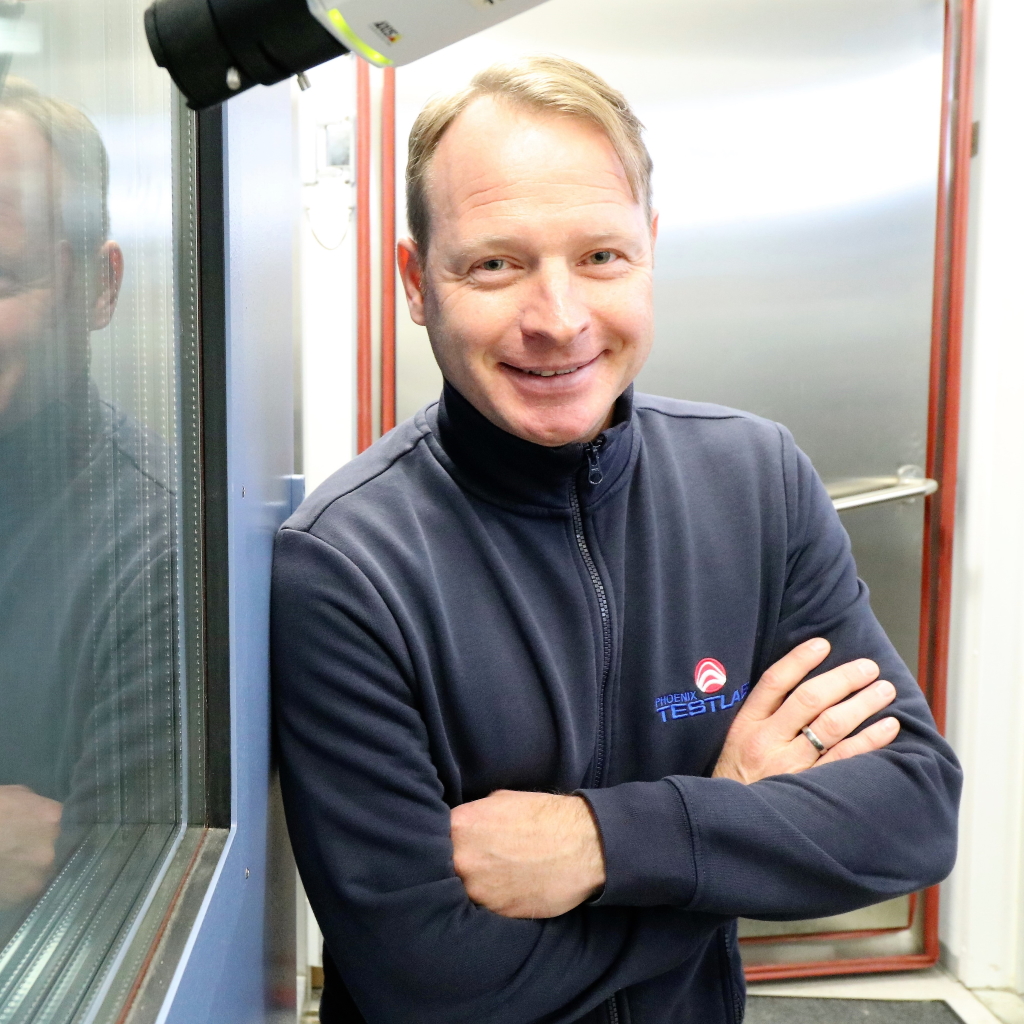
Ich lebe mit meiner Ehefrau in Bad Pyrmont. Als Ausgleich zum Job mache ich viel Sport, gehe Joggen und nehme an Volksläufen teil. Im Winter gehe ich sehr gerne Skifahren. Ruhe und Entspannung finde ich mit meiner Frau und unserem Hund im Garten.
0 Kommentare