Smart Factory – digitale Umbaupläne
Im heutigen Blog gibt euch Nihat einen Einblick in die Wertschöpfungskette einer Smart Factory bei Phoenix Contact. Er stellt euch ein Digitalisierungsprojekt aus dem Werkzeugumbau vor.
Industrie 4.0 – das ist die Produktion der Zukunft. Alles wird „smart“, nicht nur das „phone“ und die „watch“, auch unser Arbeitsalltag verändert sich im Rahmen der Digitalisierung rasant. Wir halten euch auf dem Laufenden darüber, was die vierte industrielle Revolution eigentlich bedeutet. Anhand von praxisnahen Beispielen erklären wir, wie wir den Weg der digitalen Transformation Richtung Zukunft beschreiten.
Im letzten Artikel hat Anja die Charakteristiken einer Smart Factory ausführlich beschrieben. Sie setzen sich hauptsächlich aus den Anforderungen der Zukunft zusammen. Der Kunde 4.0 wird verstärkt individuelle Produkte mit geringen Stückzahlen anfragen. Eine Smart Factory muss in der Lage sein, flexibel und wirtschaftlich auf den Kundenwunsch zu reagieren. Aber was genau bedeutet das für unsere Fertigung und im Besonderen für den Werkzeugumbau?
Großes Know-how durch hohe Fertigungstiefe
In der Produktion von Phoenix Contact haben wir eine ausgeprägte Fertigungstiefe. Über Schrauben, Klemmhülsen und Kunststoffteile bis hin zu unseren Maschinen und Werkzeugen stellen wir so gut wie alles in Eigenleistung her.
Ob wir einen oder 5.000 Stecker produzieren, die Anforderungen und Qualitätsvorgaben sind gleich. Der erste sowie auch der letzte Stecker müssen die gleiche Formgenauigkeit und die gleichen strukturellen Eigenschaften aufweisen. Das gewährleisten wir mit der hohen Prozesssicherheit unserer Kunststofffertigung. Das Herzstück bilden dabei unsere selbstgebauten Werkzeuge. Für das gesamte Produktportfolio unserer COMBICON-Fertigung haben wir 1.200 Werkzeuge, mit denen wir ca. 22.000 verschiedene Artikel herstellen können.
Der historische Werkzeugumbau
Ein Werkzeug besteht aus mehreren Kavitäten. Kavitäten sind die „Formnester“, in denen die Kunststoffelemente hergestellt werden. Die Anzahl der Formnester bestimmt, wie viele Kunststoffelemente mit jedem Spritzzyklus hergestellt werden können. Welches Kunststoffelement gefertigt wird, richtet sich nach dem Kundenwunsch. Bestellt ein Kunde z. B. einen fünfpoligen Stecker, bekommt der Werkzeugmechaniker den Auftrag für genau diese Variante. Er bestückt die Kavität mit den dazugehörigen Formeinsätzen. Das Bestücken bzw. Zusammenstellen eines Werkzeugs ist die Kernarbeit des Umbauprozesses. Bisher besteht zu jedem Umbauauftrag eine Umbauanleitung in Papierform. Papierausdrucke bringen immer die Frage nach der Aktualität mit sich. Bei 22.000 Artikeln mit den jeweiligen Umbauplänen ist es schon eine Herausforderung, die Pflege und damit die Aktualität der Dokumente sicherzustellen. Außerdem belasten Papierausdrucke unnötig die Umwelt.
Der digitalisierte Werkzeugumbau
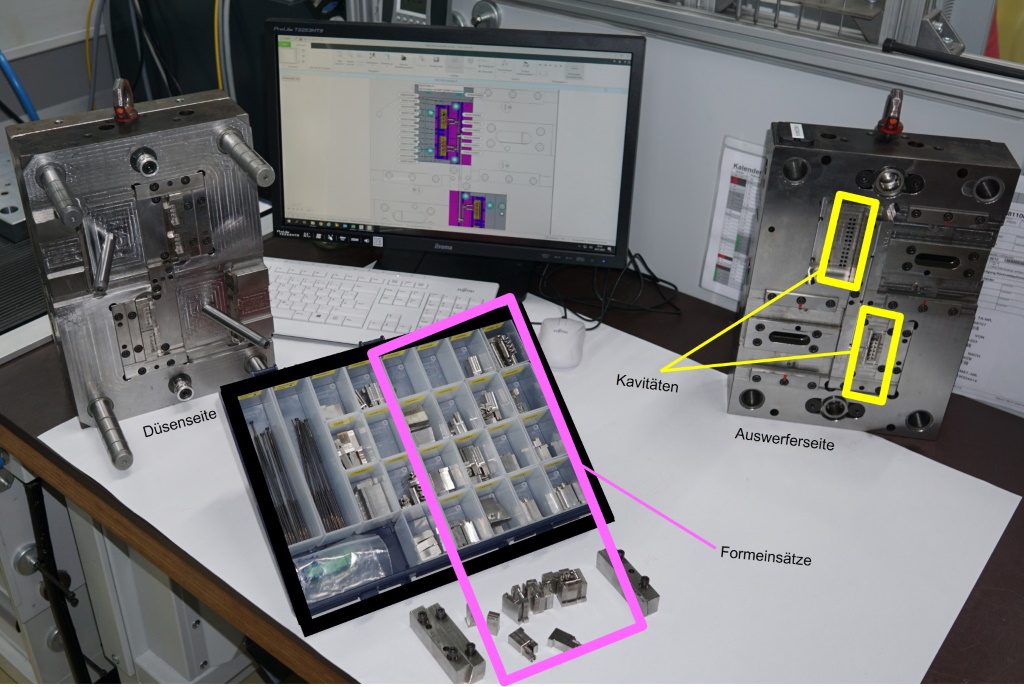
An diesem Punkt greift die Digitalisierung. Sie bietet ein großes Optimierungspotenzial, das wir mit unserem Projekt der 3D-Umbauanleitung umsetzen möchten. Änderungen an den Stammdaten sind durchgängig und bewirken, dass angebundene Prozesse und Dokumente automatisch aktualisiert werden. Das Zusammenspiel der Bauteile kann vor der Arbeitsaufführung simuliert werden. Der Mechaniker kann so vor der Ausführung auf Abweichungen reagieren. Aufwendige Rückfragen werden überflüssig und Suchzeiten für Dokumente extrem verkürzt.
Da die meisten unserer Werkzeuge bereits in 3D konstruiert wurden, bilden die digitalen Stammdaten die Basis unserer Digitalisierung. Je genauer die Stammdaten sind, umso besser ist der digitalisierte Prozess. Unsere erfahrenen Werkzeugmacher erstellen zu jeder Artikelvariante eine Umbauanleitung. In dem neuen Verfahren kann sich der Facharbeiter die einzubauenden Elemente im 3D-Modell ansehen. Der digitale Zwilling des Werkzeugs ermöglicht eine Betrachtung des Arbeitsschritts vor der Ausführung. Der Mechaniker muss keine Papierzettel mehr heraussuchen. Er hat immer die Gewissheit, dass seine Dokumente auf dem neuesten Stand sind. Dadurch bekommt er mehr Sicherheit und Ruhe in seine Arbeitsausführung.
Fazit des Projekts:
- Je genauer die Stammdaten sind, umso einfacher und besser kann ein Prozess digitalisiert werden.
- Die investierte Zeit zur Aufbereitung und Erstellung von Umbauplänen amortisiert sich relativ schnell.
- Die Umbauzeiten je Auftrag werden spürbar gesenkt.
Das Projekt ist ein gutes Beispiel, wie wir unsere Daten für die digitale Transformation nutzen. In meinen nächsten Blogbeiträgen werde ich euch von weiteren Beispielen auf unserem Weg zur Smart Factory berichten.
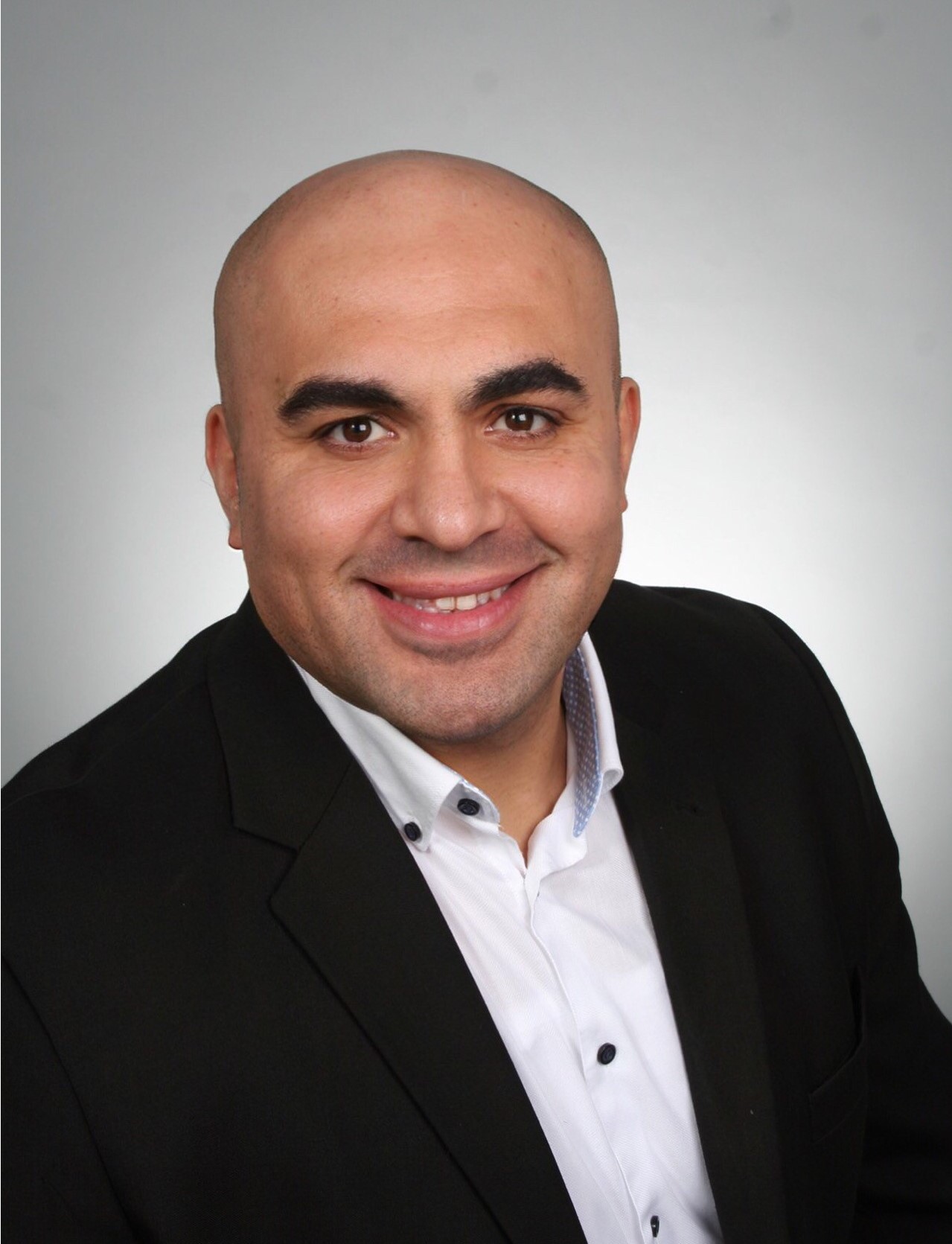
Bei Phoenix Contact betreue ich Digitalisierungsprojekte rund um die Produktion. Meine 30-jährige Produktionserfahrung hilft mir dabei, die Fertigung von gestern in die digitale Welt von morgen zu überführen. Privat merke ich auch, dass die Digitalisierung immer mehr Einzug hält. Die neuen Cardiogeräte in meinem Fitnessstudio haben z. B. tolle Work-Out-Programme.
0 Kommentare