PLCnext Technology: Festo e Phoenix Contact firmam parceria tecnológica estratégica
From |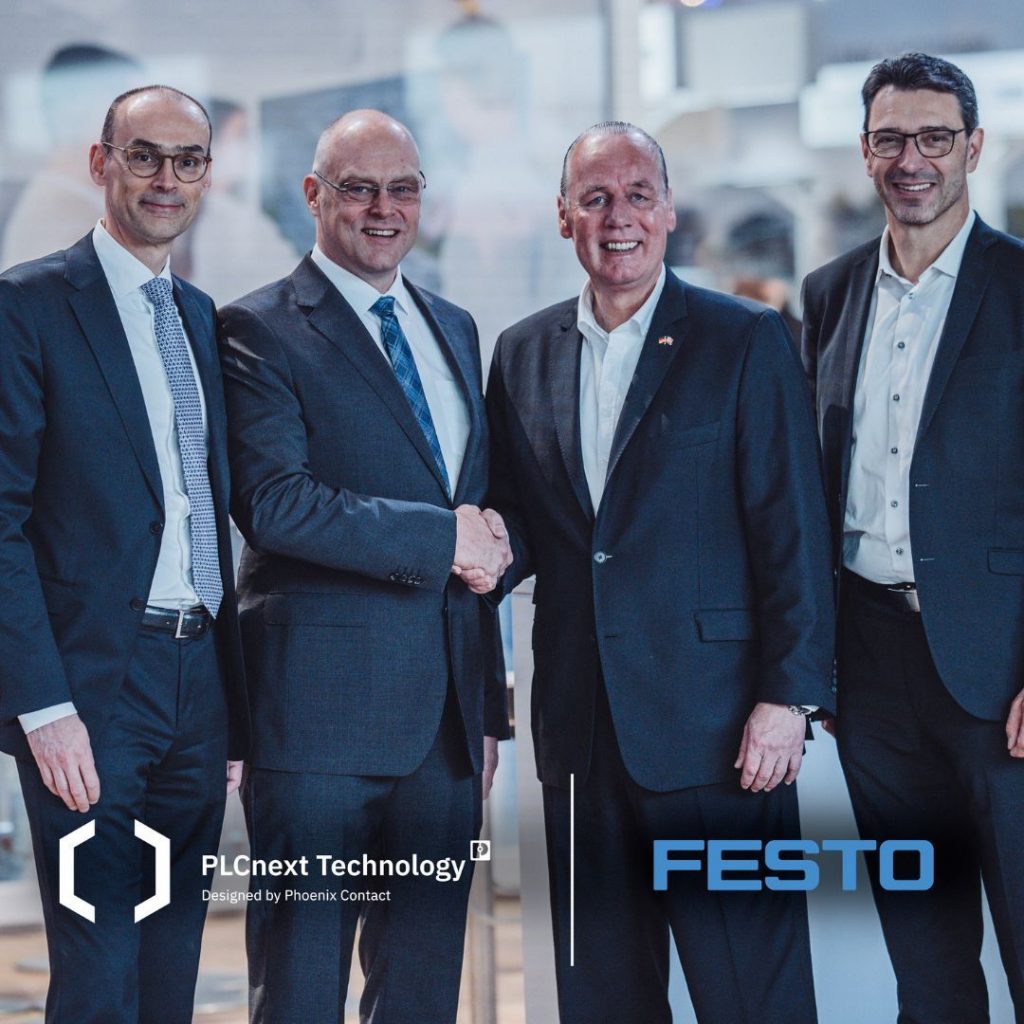
A Festo, fabricante de tecnologia de automação pneumática e elétrica, utilizará a PLCnext Technology, o ecossistema aberto para automação moderna da Phoenix Contact, em futuros dispositivos inteligentes. Isto combinará a força inovadora de ambas as empresas com o objetivo de levar a automação industrial a um novo nível. A nova geração de produtos deverá ser […]