Written by Andy Maskell, Product Manager- Safety & Networks
Safe motion monitoring has become increasingly important in machine and system design. Conventional safety technology keeps the operator away from dangerous movement by shutting down the relevant drive when a moveable guard, e.g. safety door, is opened. This usually results in the removal of power sources using contactors or other forms of power disconnection. “Safe Switch Off”.
Another example of this is Safe Torque Off, or STO, which has become common in modern drive systems. STO ensures that no power generating energy is supplied to the motor without the need for additional contactors or switch gear . This function corresponds to an uncontrolled stop in accordance with IEC 60204-1:2006 (9.2.1) and stop category 0 (Stopping by immediate removal of power to the machine actuators).
Stop categories 1 and 2 result in a controlled stop of the drive. In the case of stop category 2, energy is still supplied to the drive elements/actuators. These categories make provision for a defined method of safe stop functions usually initiated by operation of an emergency stop device.
Safe motion allows for safe movement and speed during production phases, such as machine set up, to reduce downtime and sustain the efficiency required in today’s demanding environment. Safe motion allows drive motion even with the safety door / guard open.
Of course, very specific conditions must be applied based on risk assessment that must be carried out. There are also specific standards (C Standards) that apply to certain machines, such as paper converting machinery, which precisely outline the safety requirements for relevant tasks based on the area of application. E.g safe set up speeds.
Safe Motion monitoring allows the safety logic to monitor the movement and sequences of drives to prevent a hazardous situation arising. Safe motion sensors are usually required to perform this task.
Some examples of safe motion monitoring methods are:
- Safe Operation Stop (SOS)
- Safe Limited Speed (SLS)
- Safe Speed Monitoring (SSM)
- Safe Speed Range (SSR)
- Safe Direction (SDI)
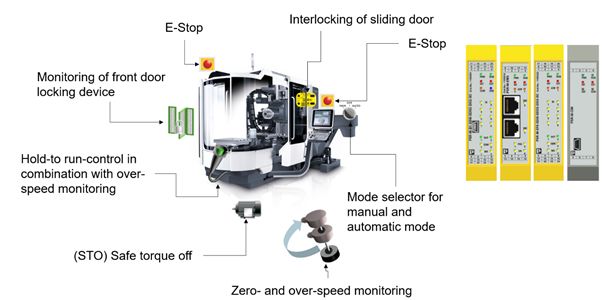
Phoenix Contact’s safe motion portfolio ranges from simple zero speed and over speed relays through to the PSRmodular configurable system.
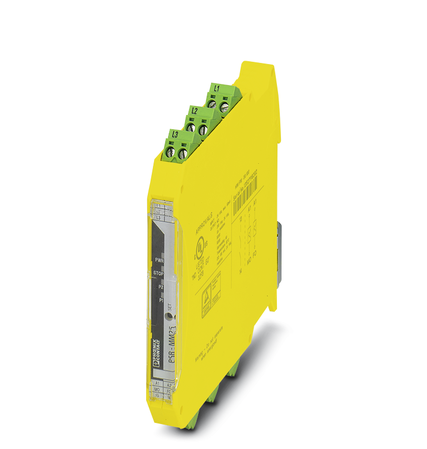
PSR-MM25
The PSR-MM25 combined with a safety door lock monitors the back emf direct from the motor ensuring the door cannot be unlocked until dangerous motion stops.
PSR-MM30
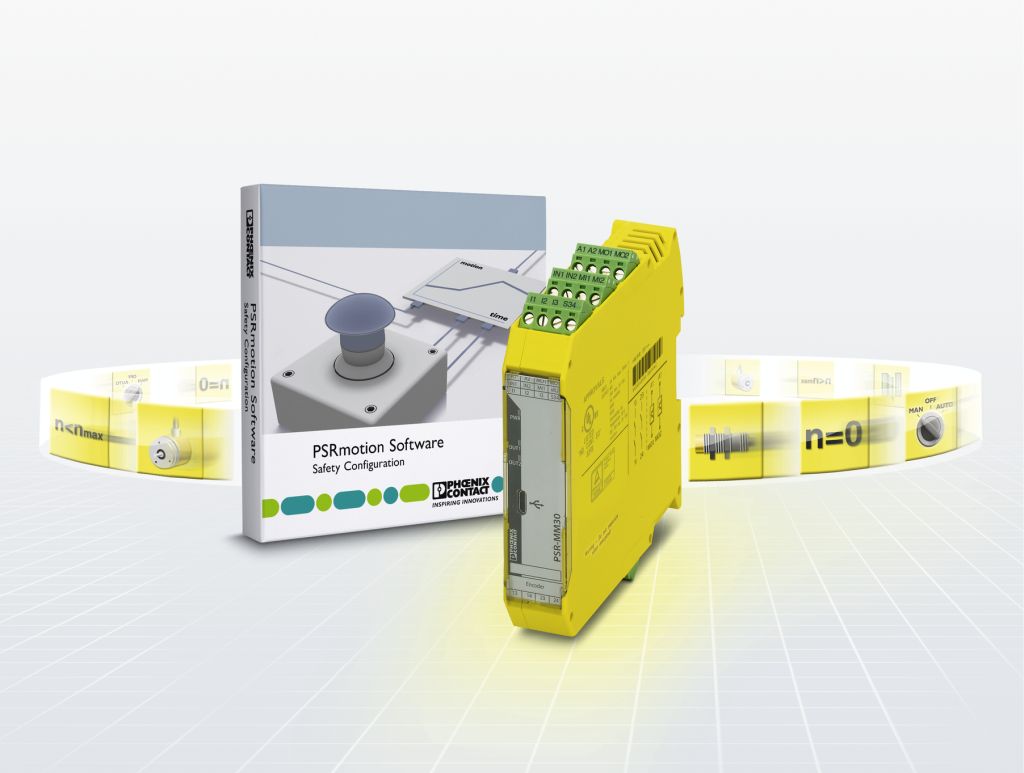
The PSR-MM30 over speed and zero speed also monitors the speed and shuts down safely in the event of hazardous speed (Motion sensors required)
PSRmodular
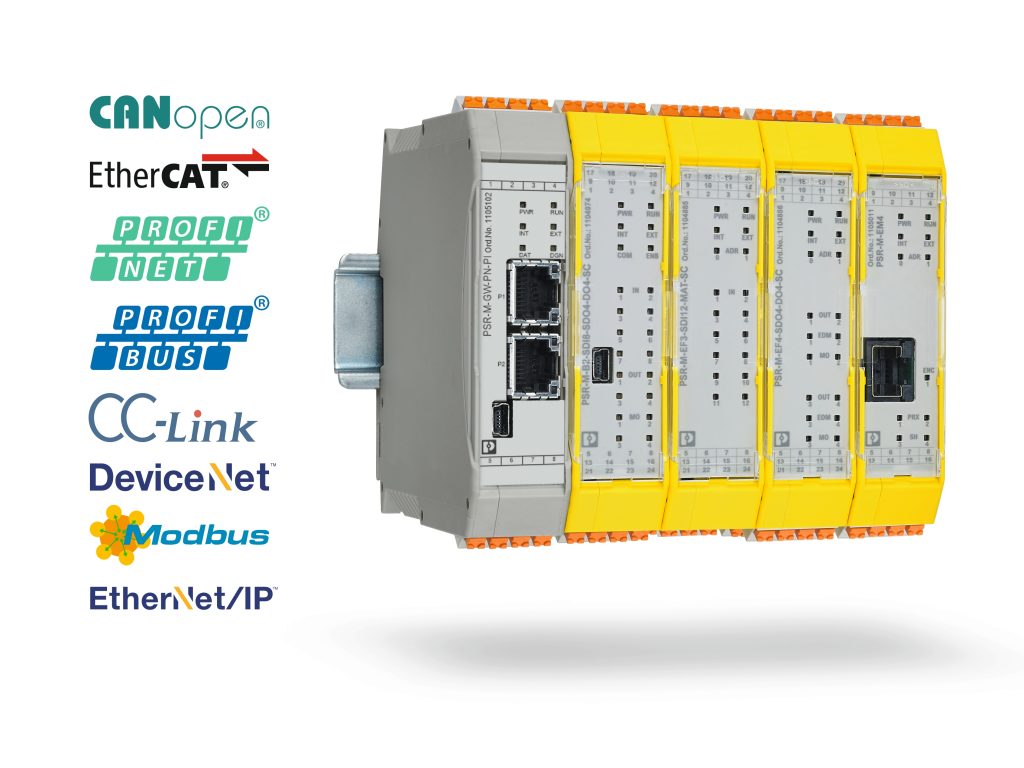
The PSRmodular configurable safety system offers optional safe extension modules for monitoring safe speed, zero speed and direction of rotation.
For safe speed monitoring we really do have a COMPLETE solution!
For more information, contact Andy on 07584 235440 or email amaskell@phoenixcontact.com