Written by Scott Mulholland, Product Manager- Industrial Components
I’ve had a number of queries recently regarding coding for our Heavycon range of heavy duty connectors. Coding can become a good idea when your application has a number of similar, or identical, connectors in close proximity like the ones on the side of this panel in this image:
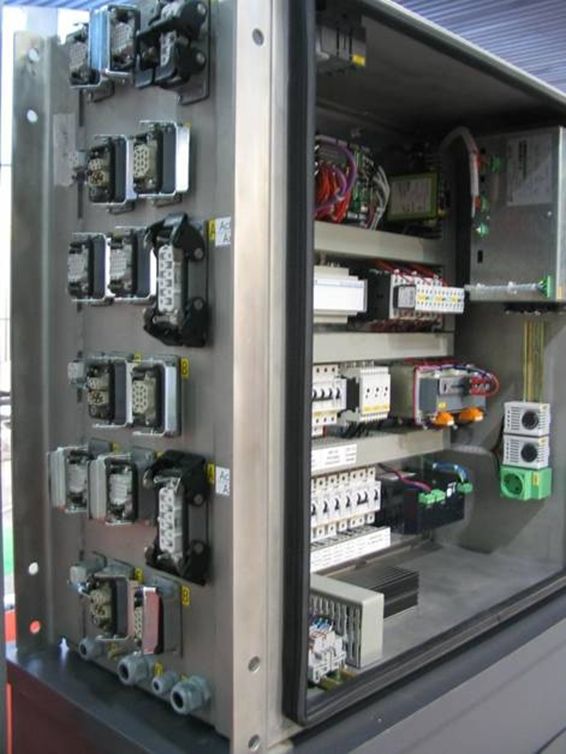
I am sure that you can appreciate the problems (if not damage) that could occur by placing the wrong connector hood on the wrong base. Often, customers understandably number the hoods and bases (so hood 1 goes to base 1 etc) which is very useful but this does not physically stop a distracted operative from placing hood one onto base 2 for instance. This is where a coding solution would do just that i.e. coding would physically make the ‘mis-mating’ of the wrong hoods and bases.
Like most effective solutions, coding is a simple concept. It’s not that it’s complicated, but the large number of Heavycon connector components in range means that there are also a high number of coding part numbers that relate to the different size Heavycon inserts/housings.
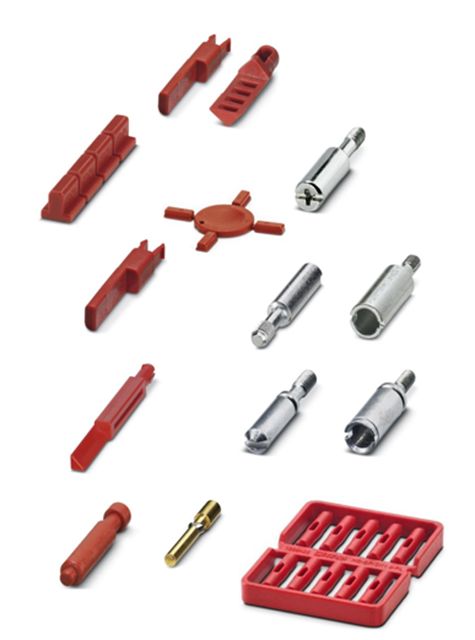
So, I’d like to clarify the issue. There’s a lot of information below, but that’s only because we have to have the appropriate coding elements for the inserts that we’re using. If you know what insert you are using, you’re half way there on determining which coding elements you’ll need. Our coding elements look like this (see right).
Straight away, we can see that we have two approaches to coding. The red plastic coding elements are very cost effective and much quicker to fit into your connectors, but the down side is the number of codings (or paired hoods and bases) that can be achieved is limited. The metal coding pins are more expensive, take more time to fit, but offer a higher number of codings that can be achieved. In fact, to fit the metal pins, you have to remove the retaining screws from the corner of a connector insert and replace with a coding pin, so this can prove time consuming. Whereas the red plastic codings are inserted into the inserts without having the need to remove and screws, so, much quicker to apply.
RED Plastic Coding Pin Solution
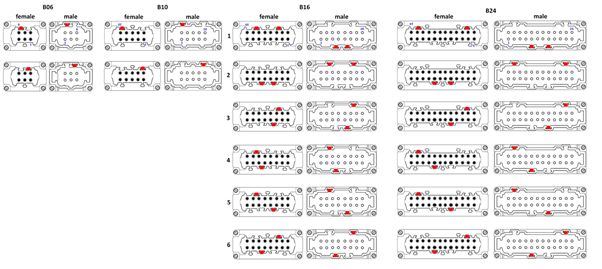
The plastic coding saves time and money but the combination number that can be achieved is limited.
Metal Coding Pin Solution
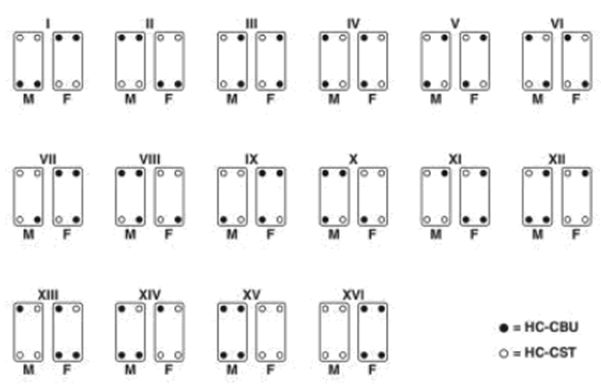
Here you have x16 variants, but with the metal coding the you must buy x8 metal coding pins (one for each fixing screw position) and then you must unscrew each screw and then screw in each coding. This takes a couple of minutes for each connector pair.
I told you there was a lot of information but the concept is straightforward. Firstly, identify which insert size you are using e.g. a B series 16 way, B16 such as our part 1407732. Then look on our website on the accessories ‘tab’ and filter on coding elements. This will list ALL of the compatible coding elements suitable for that insert size:
Then you need to determine whether to use plastic or metal pins. If it’s a small number of coded connectors that you need, red plastic pins should suffice, saving you time and money. If it’s a higher number of coded connectors that you need to achieve, metal coding pins are the way to go. Remember, they are more expensive and take a more time to fit but when considered against damage that could result from not coding (potentially catastrophic to the panel/machine), the assurance they give is good value for money.
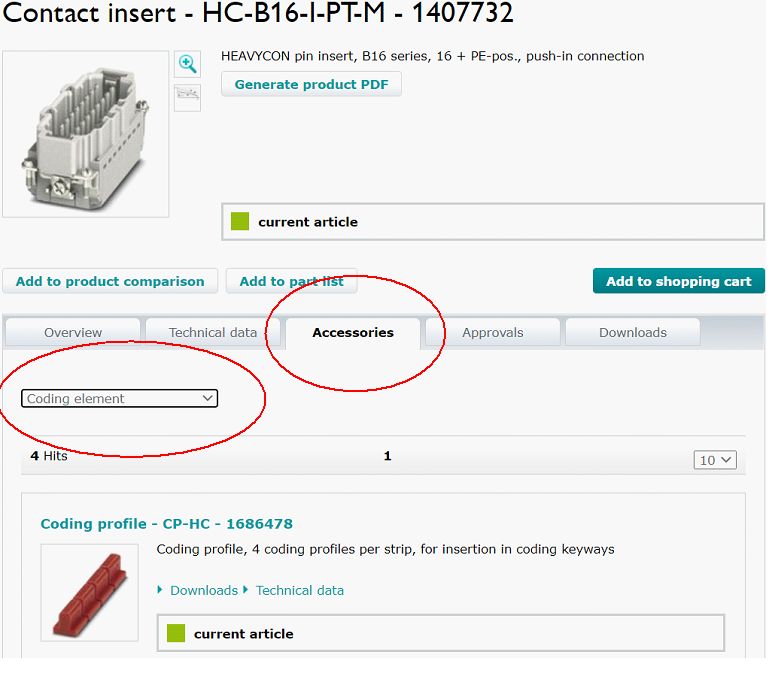
Above I have detailed the steps that you would need to take to achieve an effective coding solution.
I have placed an appendix below of all of the series insert/housing sizes and their respective coding parts, but, as I say, if you follow the steps above, you should be fine.
As always though, I’d welcome any questions on this subject or please contact me if you’d like a little more guidance on Heavycon coding: Email- smulholland@phoenixcontact.com or tel: 07908 583375